Core Formation Cycle One

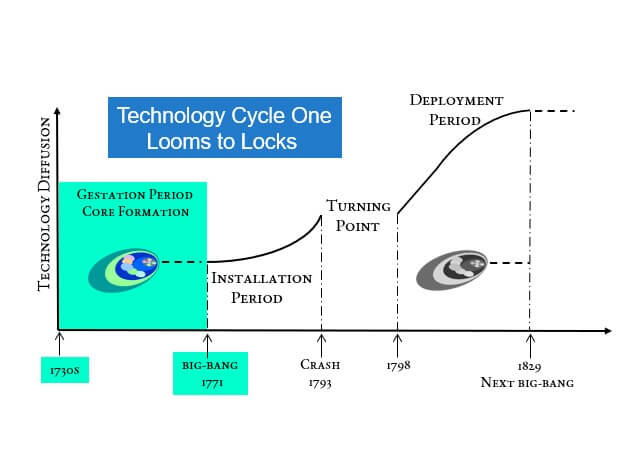
The Core Formation Period of the First Technology Cycle (1730-1771):
The Industrial Revolution did not emerge overnight as a sudden transformation of human civilization. Instead, deliberate technological and economic development spanning decades culminated in this revolutionary period. Carlota Perez terms this foundational phase the Gestation Period. It is a “Core Formation Period,” a systematic process that established the groundwork for industrial transformation.
This remarkable period lasted roughly roughly four decades. During these crucial decades, innovators, entrepreneurs, and financiers established the technological infrastructure, economic mechanisms, and industrial frameworks to power humanity’s first major technology surge. The period created not just individual innovations but entire systems of production, distribution, and finance.
Rather than comprising random innovations scattered across time, the Core Formation Period followed systematic development patterns. Five phases characterize this transformative process: initial ripples of unrelated innovations, coalescence around identified bottlenecks, emergence of revolutionized industries, competitive imitation and systematic improvement, and comprehensive financial reorientation toward industrial ventures.
Understanding this period reveals how seemingly chaotic technological change actually follows predictable patterns and developmental stages. Subsequent technology cycles would repeat these same fundamental phases, suggesting universal principles governing technological revolution. Contemporary observers could hardly recognize the systematic nature of changes occurring around them, yet historical analysis reveals remarkable consistency in how major technological transformations unfold.
Phase 1: Initial Ripples – Unrelated Innovations (~1730s-1740s)
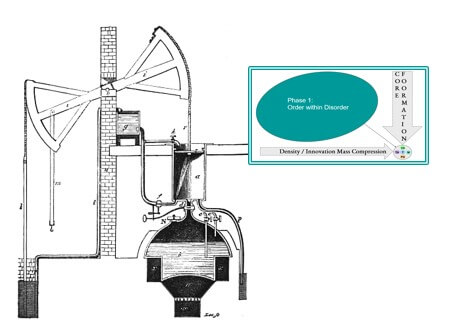
Following the invention of the Newcomen atmospheric engine, it was improved after 1712. A version of it is pictured on the left. It was an early steam engine used to pump water out of mines.
Scattered innovations across completely disparate sectors characterized the Core Formation Period’s opening phase. Inventors and entrepreneurs worked in apparent isolation during these early decades, pursuing solutions to specific problems within their immediate spheres of influence. These “initial ripples” represented the earliest stirrings of what would eventually become a coherent technological revolution, though contemporaries could hardly recognize their ultimate significance or interconnected potential.
John Kay invented the Flying Shuttle in 1733, perfectly exemplifying this pattern of isolated innovation during the period’s earliest years. Kay’s ingenious device doubled weaving speed by allowing single operators to send shuttles across much wider looms without requiring assistance from additional workers. While the Flying Shuttle would eventually revolutionize textile production throughout England, it initially appeared as merely another incremental improvement in an ancient craft that had remained largely unchanged for centuries.
Simultaneously, Abraham Darby continued refining coke usage for iron smelting at his innovative Coalbrookdale works. Building systematically on his father’s earlier experimental work, Darby perfected advanced techniques for producing high-quality iron using coke instead of increasingly scarce and expensive charcoal. This crucial development addressed critical resource constraints that threatened iron production expansion, but it remained confined mainly to metallurgical applications with little apparent connection to developments in other sectors.
Tull continues
Meanwhile, Jethro Tull continuously refined his revolutionary seed drill throughout the 1730s, improving upon his original 1701 invention. Tull’s sophisticated device allowed farmers to plant seeds in precise rows at optimal depths, dramatically improving crop yields while reducing seed waste. The innovation solved specific agricultural problems related to food production efficiency, but it operated entirely independently of textile, metallurgical, or mechanical developments occurring simultaneously.
Thomas Newcomen had developed the atmospheric steam engine in 1712 and gradually improved its performance through the following decades. Engineers primarily employed this groundbreaking technology for draining water from increasingly deep coal mines. While absolutely crucial for expanding coal mining operations, the steam engine remained a highly specialized tool rather than general-purpose technology with broader industrial applications.
Quantitative advancements
Leonhard Euler advanced crucial mathematical principles that would later prove essential for engineering calculations and mechanical design. Throughout the 1730s and 1740s, Euler published groundbreaking theoretical work on mechanics, fluid dynamics, and mathematical analysis. However, these theoretical advances remained largely confined to academic circles, showing no immediate practical applications in emerging industrial processes.
Clockmakers like John Harrison pursued precision timekeeping innovations entirely independently of other technological developments during this period. Harrison spent decades perfecting mechanical chronometers specifically for maritime navigation, addressing critical problems in global trade and ocean exploration. His meticulous work operated completely separately from textile, metallurgical, steam power, or agricultural innovations occurring simultaneously.
Glassmakers also developed improved techniques for producing clearer, more consistent glass during the 1730s and 1740s. These innovations primarily served traditional markets for windows, bottles, and decorative items. Craftsmen had no way of anticipating the massive demand for industrial glazing that would emerge as factories required large windows for natural lighting.
In addition, early chemical experiments began yielding practical results for specific industrial applications. Innovators discovered improved methods for producing acids, alkalis, and other chemicals essential for textile processing. These developments remained confined to specialized applications without broader industrial integration or systematic expansion.
These scattered innovations across multiple sectors shared several essential characteristics that distinguished them from later phases. Practical problem-solving rather than theoretical scientific advancement primarily drove their development. Hands-on craftsmen and practical entrepreneurs, rather than academic researchers or systematic investigators, created these innovations. Most importantly, they operated completely independently of one another, creating isolated pockets of improvement without yet forming integrated technological systems or recognizing broader industrial potential.
Phase 2: Coalescence to Solve Bottlenecks (~1740s-1750s)
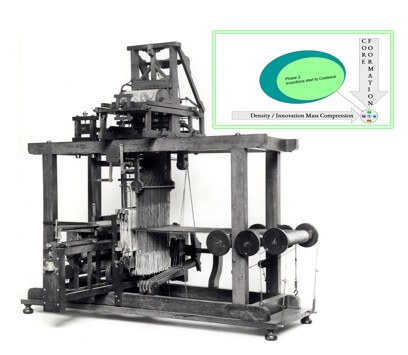
The second phase witnessed crucial shifts from isolated innovations to systematic recognition of interconnected bottlenecks that threatened further progress. As initial technological ripples spread through their respective sectors, they created significant imbalances and constraints that demanded coordinated solutions rather than isolated improvements. This period marked the first recognition that technological progress required systematic rather than piecemeal approaches.
The textile industry provided the clearest and most dramatic example of this evolving dynamic. Kay’s Flying Shuttle had dramatically increased weaving speed, but this improvement created acute yarn shortages that threatened to limit the technology’s benefits. Weavers could now produce finished cloth much faster than spinners could supply the necessary thread, creating severe bottlenecks that required systematic solutions rather than isolated improvements.
Pictured on the left was Vaucanson’s invention from 1745, the first automated loom.
Bottlenecks
This textile bottleneck extended beyond purely technical issues to encompass broader economic and organizational challenges. The entire textile production system required fundamental re-balancing to capture the Flying Shuttle’s revolutionary potential. Traditional spinning methods, which had adequately served slower weaving processes, proved completely inadequate for the new production rates that mechanical weaving enabled.
Similarly, improvements in iron production revealed fundamental resource constraints that threatened further industrial development. The increasing use of coke smelting had solved immediate charcoal shortage problems, but it created entirely new demands for efficient coal transportation and more sophisticated furnace designs. The iron industry discovered that technological improvements in one specific area inevitably created pressures for innovation in multiple related areas.
Transportation emerged as another critical bottleneck limiting industrial expansion during this crucial period. As manufacturing output increased steadily and regional specialization developed, the movement of raw materials and finished goods became increasingly problematic. Traditional road transport systems proved completely inadequate for the growing volumes of heavy materials like coal, iron ore, and finished manufactured goods.
The power generation bottleneck proved equally significant for industrial development. While water wheels provided reliable energy for many manufacturing processes, they tied industrial development to specific geographical locations near suitable water sources. Seasonal variations in water flow subjected production to unpredictable constraints, while atmospheric steam engines offered alternatives severely limited by their inefficiency and high operating costs.
Moreover, the glass industry revealed systematic bottlenecks during this transformative period. Increased demand for window glass from expanding textile mills strained traditional glassmaking methods beyond their capacity. Manufacturers discovered that industrial buildings required glass production techniques far beyond those traditionally used for bottles and household items. The scale and consistency requirements of industrial glazing demanded entirely new approaches to glass manufacturing.
Chemical industry
The chemical industry faced unprecedented demands for industrial processes that traditional methods could not possibly satisfy. Textile bleaching and dyeing operations required chemicals in quantities that traditional apothecary methods could not supply reliably or economically. Furthermore, soap production for industrial cleaning processes created entirely new scale requirements that existing chemical knowledge and production methods could not address adequately.
Transportation networks also exposed critical limitations in skilled labor availability that threatened industrial expansion. Canal construction projects revealed severe shortages of experienced engineers, surveyors, and construction specialists capable of managing large-scale infrastructure projects. Consequently, the industry recognized that technological advancement required parallel development of technical education and comprehensive apprenticeship programs.
Labor shortages extended beyond technical specialists to include skilled craftsmen capable of operating and maintaining increasingly complex machinery. The transition from traditional craft production to mechanized manufacturing required workers with entirely new skill sets that existing training systems could not provide adequately.
Raw material supply chains revealed additional bottlenecks as industrial demand increased. Traditional suppliers of cotton, wool, iron ore, and other essential materials lacked the capacity and organization necessary to reliably serve expanding industrial operations. This created urgent needs for more systematic approaches to supply management and raw materials.
Quality control emerged as another systematic bottleneck as production volumes increased. Traditional craft methods relied on individual skill and experience to maintain quality standards. However, larger-scale production required systematic quality control methods that could ensure consistency across much larger volumes of output.
These interconnected bottlenecks proved crucial because they revealed the fundamentally systemic nature of technological change. Individual innovations could not reach their full potential without complementary developments in multiple related areas. This recognition marked a fundamental shift from viewing technology as a collection of independent tools to understanding it as integrated systems requiring coordinated development across multiple sectors simultaneously.
Phase 3: Emergence of New & Revolutionized Industries (~1750s-1760s)
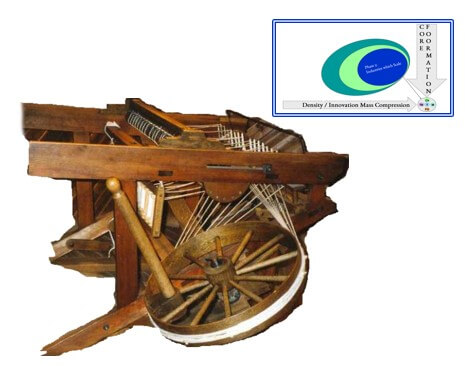
The third phase represented the emergence of systematic industrial innovation as inventors and entrepreneurs began developing technologies specifically designed to address the bottlenecks encountered during the previous phase. This period witnessed the birth of core industries that would define the first technology cycle and establish templates for industrial organization that would persist for generations. Rather than isolated improvements, this phase produced integrated solutions to systematic problems.
James Hargreaves invented the revolutionary Spinning Jenny in 1764 (pictured on the left), directly addressing the severe yarn shortages that Kay’s Flying Shuttle had created in textile production. It represented a fundamental shift in thinking about industrial problems.
New thinking
Instead of simply improving existing methods, Hargreaves created entirely new approaches that could operate at scales matching the demands created by previous innovations. His machine demonstrated how systematic thinking about industrial bottlenecks could yield revolutionary rather than incremental solutions.
The Jenny allowed single operators to spin multiple threads simultaneously, dramatically increasing yarn production and beginning to restore balance to textile manufacturing systems. More importantly, Hargreaves conceived his invention not as an isolated improvement but as part of systematic solutions to industry-wide constraints that threatened further progress.
Richard Arkwright patented the Water Frame in 1769, taking systematic approaches to industrial organization even further than previous innovations. Arkwright didn’t simply invent new spinning machines; he created comprehensive factory systems organized around continuous production processes that integrated multiple technologies within purpose-built facilities. His mills combined spinning machinery, power transmission systems, and organized labor within structures specifically designed for industrial production.
The Water Frame system established the template for industrial manufacturing that would define the coming century. Arkwright’s innovations extended beyond mechanical improvements to encompass systematic approaches to labor organization, quality control, and production scheduling. His factories demonstrated how technological innovation required parallel innovations in organizational structure and management systems.
Watt
James Watt’s improvements to the steam engine culminated in his separate condenser patent of 1769, transforming specialized mining equipment into general-purpose industrial technology. Watt’s innovations dramatically improved steam engine efficiency while making the technology suitable for a wide variety of manufacturing applications. This development proved crucial because it freed industrial production from dependence on water power and specific geographical locations.
Watt’s steam engine innovations extended far beyond mechanical improvements to encompass systematic approaches to commercialization and technology transfer. His partnership with Matthew Boulton created new models for scaling technological innovation that combined technical expertise with financial resources and manufacturing capabilities.
Canal construction experienced unprecedented expansion during this period, exemplified by the Bridgewater Canal completed in 1761. This groundbreaking project connected the Duke of Bridgewater’s coal mines directly to Manchester, demonstrating the enormous economic potential of purpose-built industrial infrastructure. The canal reduced coal transportation costs by more than half, proving that systematic infrastructure investment could multiply the benefits of other technological innovations.
The Bridgewater Canal success triggered systematic recognition of transportation infrastructure’s crucial role in industrial development. Subsequent canal projects built upon this model, creating integrated transportation networks that could support industrial expansion across entire regions rather than isolated locations.
Precision instrument making advanced significantly through innovators like John Harrison with his marine chronometer developments. While seemingly specialized, precision instruments proved crucial for the navigation, surveying, and measurement requirements of an increasingly complex industrial economy. These instruments enabled the accurate mapping and planning necessary for large-scale infrastructure projects.
Factory systems
During this transformative phase, Joseph Wedgwood revolutionized pottery manufacturing through systematic industrial organization. Wedgwood established the first pottery factory that integrated multiple production stages under one roof, from clay preparation through firing and finishing. His innovations transformed ceramic production from individual craftsmanship into coordinated industrial processes that could achieve consistent quality at unprecedented scales.
Wedgwood’s factory system demonstrated how systematic organization could multiply productivity while maintaining quality standards. His innovations extended beyond production methods to encompass systematic approaches to product design, marketing, and distribution that established new standards for industrial organization.
Concurrently, Matthew Boulton created the Soho Manufactory, pioneering mass production techniques for metal goods that would influence manufacturing throughout the industrial period. Boulton organized production lines that could manufacture buttons, buckles, and decorative items at unprecedented scales while maintaining quality standards. His factory demonstrated how systematic organization could multiply individual craftsmen’s productivity through coordinated production systems.
The Soho Manufactory became a model for industrial organization that attracted visitors from across Europe. Boulton’s innovations in production planning, quality control, and worker organization established principles that would influence industrial development for generations.
Additionally, the brewing industry underwent systematic transformation during this crucial decade. Commercial brewers developed standardized processes that could produce consistent beer quality across multiple locations and production batches. These innovations required entirely new approaches to quality control, ingredient sourcing, and distribution that previous brewing methods had never addressed systematically.
Brewing innovations extended beyond production methods to encompass systematic approaches to supply chain management and product distribution. The industry developed new methods for managing raw material supplies, controlling fermentation processes, and maintaining product quality during transportation and storage.
Textiles
Textile machinery manufacturing emerged as a distinct industry during this period, producing specialized equipment for the expanding textile sector. Machine builders developed systematic approaches to manufacturing spinning wheels, looms, and related equipment that could meet the growing demand from textile manufacturers.
The machine tool industry began developing specialized equipment for manufacturing other machines, establishing the foundation for systematic industrial expansion. These innovations enabled the production of increasingly complex machinery with greater precision and reliability than traditional craft methods could achieve.
Coal mining operations became increasingly systematic during this period, developing new methods for extraction, transportation, and processing that could meet growing industrial demand. Mining entrepreneurs invested in specialized equipment, systematic exploration methods, and improved safety systems that transformed coal mining from traditional craft to industrial operation.
These revolutionary developments shared several key characteristics that distinguished them from earlier phases of technological development. Inventors conceived them as systematic solutions to specific bottlenecks rather than isolated improvements to existing methods. They integrated multiple technologies and processes rather than focusing on single innovations. Most importantly, they began creating the industrial infrastructure and organizational models that would define mature technology cycles and establish the foundation for sustained industrial growth.
Phase 4: Imitation and Improvement (~1760s-early 1770s)
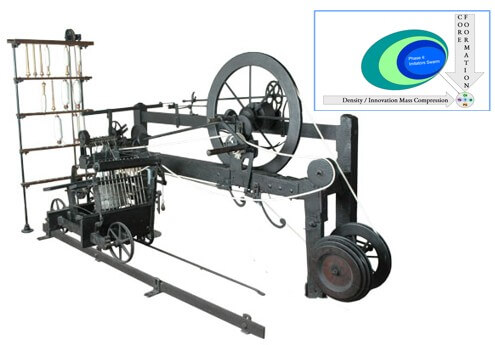
Competitive imitation and systematic improvement of breakthrough innovations from the previous phase characterized the fourth phase of the Core Formation Period. This period witnessed the geographical diffusion of new technologies and the development of competing approaches to identical industrial challenges. Rather than simply copying existing innovations, entrepreneurs and inventors created variations that adapted core technologies to different conditions and markets.
Samuel Crompton developed the Spinning Mule in the late 1770s, building on extensive work he had begun during the 1760s. Crompton’s innovation represented more than simple imitation; he combined the best features of both the Spinning Jenny and the Water Frame, creating hybrid technology that produced higher-quality thread than either predecessor. The Mule demonstrated how competitive pressures drove continuous technological advancement through innovative synthesis rather than mere replication.
Crompton’s approach illustrated how competitive improvement could yield superior results through systematic analysis of existing technologies. His machine incorporated mechanical principles from multiple sources while adding original innovations that addressed limitations in previous designs. This pattern of competitive synthesis would become characteristic of technological development throughout the industrial period.
Henry Cort’s development of the puddling process represented similar patterns of systematic improvement in metallurgical applications. Building upon existing iron refining techniques, Cort created new methods for producing high-quality wrought iron more efficiently than any previous approach. His innovations responded directly to the growing demand for iron created by other industrial developments, illustrating how technological progress in one sector consistently stimulated innovation in related areas.
Cort’s puddling process innovations extended beyond immediate technical improvements to encompass systematic approaches to production planning and quality control. His methods enabled iron producers to achieve consistent quality while significantly reducing production costs, establishing new standards for metallurgical operations.
Canal expansion
The canal network expansion following the remarkable success of the Bridgewater Canal demonstrated how successful innovations quickly spread through systematic imitation and local adaptation. Entrepreneurs launched multiple canal projects throughout England, each carefully adapting basic engineering concepts to local geographical and economic conditions. This diffusion process proved crucial for creating the comprehensive transportation infrastructure that mature industrial economies would require.
Canal construction projects developed systematic approaches to engineering, financing, and management that standardized infrastructure development across different regions. These innovations in project organization and execution established templates that would influence infrastructure development far beyond the canal era.
Steam engine technology spread through similar processes of licensing and systematic adaptation. The Boulton and Watt partnership, formally established in 1775 but based on extensive earlier collaboration, created systematic approaches to commercializing and improving steam technology. Their model of licensing patents while providing ongoing technical support became a template for technology diffusion that subsequent cycles would repeatedly adopt.
The Boulton and Watt partnership demonstrated how systematic commercialization could accelerate technology diffusion while maintaining quality standards. Their approach combined patent protection with technical support services, creating sustainable business models for technology transfer that would influence future industrial development.
Textile machinery
Regional variations in textile machinery illustrated how competitive imitation consistently drove innovation rather than mere replication. Different manufacturing centers developed their own adaptations of spinning technologies, optimized for local labor conditions, raw material availability, and market requirements. This geographical diversity in technological development created robust foundations for industrial systems by preventing dangerous dependence on any single approach or location.
Edmund Cartwright observed the success of spinning innovations and developed the power loom specifically to address weaving bottlenecks that improved spinning had created. Cartwright recognized that dramatic improvements in spinning capacity had created new constraints in cloth production that required systematic solutions. His mechanical loom represented competitive responses to technological imbalances that earlier innovations had inadvertently created.
Cartwright’s power loom development demonstrated how systematic observation of technological bottlenecks could guide innovation toward areas of greatest need. His approach illustrated how competitive improvement could address systemic constraints rather than simply replicating existing successful technologies.
Simultaneously, coal mining entrepreneurs developed systematic improvements to extraction methods that built upon successful techniques from different regions. Mine operators carefully studied effective extraction techniques and systematically adapted them to local geological conditions and resource availability. These competitive improvements dramatically increased coal output necessary for expanding industrial operations throughout England.
Coal mining innovations extended beyond extraction methods to encompass systematic approaches to transportation, processing, and safety that established new standards for extractive industries. These improvements created the reliable coal supplies that other industrial sectors required for sustained expansion.
Road construction
Furthermore, road construction techniques evolved through competitive imitation of successful infrastructure projects. Turnpike trusts systematically studied effective road-building methods and adapted them across different regions with varying geological and economic conditions. John Metcalf pioneered road construction techniques that other builders quickly copied and systematically refined throughout northern England.
Road construction innovations established systematic approaches to infrastructure development that would influence transportation improvements far beyond the immediate period. These techniques created more reliable transportation networks that supported industrial expansion across broader geographical areas.
Textile finishing processes underwent systematic improvement as manufacturers competed to produce higher-quality fabrics. Innovations in dyeing, bleaching, and fabric treatment created new standards for textile quality while reducing production costs. These improvements demonstrated how competitive pressures consistently drove technological advancement throughout entire industrial sectors.
Machine tool manufacturing developed systematic approaches to producing increasingly precise and reliable equipment for other industries. Specialized tool makers created innovative methods for manufacturing spinning wheels, looms, and other industrial equipment that could meet growing demand while maintaining quality standards.
The imitation and improvement phase proved crucial because it transformed breakthrough innovations from isolated successes into systematic industrial capabilities available across broad geographical areas. Competition between different approaches drove rapid technological advancement while geographical diffusion created resilient industrial networks that could withstand local disruptions and continue expansion.
Phase 5: Financial Reorientation Toward Industrial Ventures (late 1760s-1771)
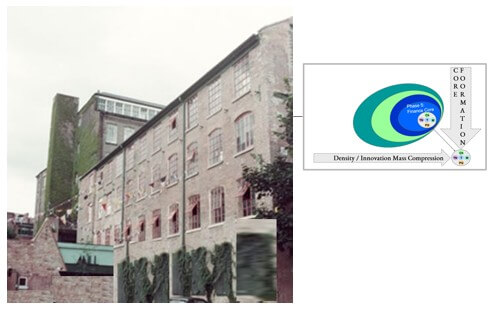
Arkwright’s financing innovations extended beyond capital raising to encompass systematic approaches to production planning, cost control, and profitability analysis. His methods established new standards for industrial financial management that would influence manufacturing development across multiple sectors.
In the 1760s, he formed partnerships to fund the obtaining of patents for his designs. He would build the world’s first cotton factory in Nottingham, England. Arkwright found two partners in John Smalley and David Thornley. A patent was obtained in 1769 with their backing, and with two more partners, Jedediah Strutt and Samuel Need, they set up a horse-powered mill at the bottom of Woolpack Lane in Nottingham. That is building seen to the left.
Horsepower would not scale
Horsepower, however, proved expensive as well as unfeasible for large-scale production. Arkwright was resolved to use water power and, in 1771, began to build a water-powered mill at Cromford in Derbyshire. It is his Cromford Mill rather than his Nottingham Mill, which is generally discussed as the first ‘factory’ due to Cromford’s outsized impact on the Industrial Revolution. The opening was the Bib-Bang moment, which launched the first technology cycle.
The final phase of the Core Formation Period witnessed fundamental shifts in financial systems and investment patterns as capital began flowing systematically toward industrial ventures rather than traditional commercial and agricultural investments. This comprehensive reorientation provided the essential financial foundations necessary to support the massive scaling of industrial operations that would characterize the Installation Period beginning in 1771.
The partnership model that Boulton and Watt pioneered represented entirely new approaches to financing technological innovation that would influence industrial development for generations. Rather than relying on individual inventors working in isolation or traditional merchant capital focused on commercial trading, this innovative model systematically combined technical expertise with financial resources in structured partnerships specifically designed to commercialize and scale new technologies effectively.
Boulton and Watt’s partnership extended beyond simple financial arrangements to encompass systematic approaches to technology transfer, quality control, and market development. Their model demonstrated how financial innovation could accelerate technological diffusion while maintaining standards and protecting intellectual property rights.
Arkwright’s systematic approach to financing textile mills illustrated another crucial development in industrial finance that would establish templates for manufacturing investment. His mills required substantial upfront investment in specialized buildings, complex machinery, and working capital—investment requirements far beyond what traditional craft production had ever demanded. Arkwright pioneered innovative methods for attracting investment partners and organizing mill financing that would become standard practice throughout the textile industry.
Canal investment
Canal investment represented perhaps the clearest example of comprehensive financial reorientation toward industrial infrastructure development. Subscription-based investment societies systematically pooled capital from multiple investors to finance canal projects that individual merchants or local communities could never have afforded independently. These sophisticated organizations developed systematic methods for evaluating projects, managing construction, and distributing returns to investors.
Canal investment societies created new financial instruments and legal structures that would influence infrastructure financing far beyond the canal era. Their innovations in project evaluation, risk management, and investor relations established templates for systematic infrastructure development that would support industrial expansion for generations.
The insurance industry’s systematic adaptation to industrial risks demonstrated how traditional financial institutions evolved to support entirely new economic activities. Lloyd’s of London systematically expanded its coverage to include industrial facilities, complex machinery, and manufactured cargo, developing entirely new methods for assessing and pricing risks with no historical precedent. This evolution proved absolutely essential because industrial ventures involved risk profiles fundamentally different from traditional commercial activities.
Insurance innovations extended beyond risk assessment to encompass systematic approaches to loss prevention and claims management. The industry developed new methods for evaluating industrial hazards and supporting safety improvements that reduced risks while enabling continued industrial expansion.
Country banks played increasingly important roles in financing local industrial development throughout this crucial period. These specialized institutions systematically developed expertise in evaluating industrial ventures and providing the credit necessary for expanding manufacturing operations. The growth of industrial banking represented crucial shifts from commercial finance focused on trading activities to production finance specifically designed to support manufacturing expansion.
Country banks created new lending instruments and evaluation methods specifically designed for industrial borrowers. Their innovations in credit assessment and loan management established systematic approaches to industrial finance that would support manufacturing development across England.
Joint stock companies
Joint-stock companies emerged as crucial vehicles for financing large-scale industrial projects that individual investors could never have supported independently. These innovative organizations systematically pooled investor capital to fund ventures requiring unprecedented levels of investment in specialized equipment and infrastructure. Moreover, joint-stock structures provided legal frameworks for managing complex industrial partnerships that traditional business forms could not accommodate.
Joint-stock companies developed systematic approaches to corporate governance and investor relations that would influence business organization far beyond the immediate period. Their innovations in management structure and financial reporting established templates for industrial organization that would support sustained economic growth.
Insurance brokers developed highly specialized policies for industrial equipment and processes during these transformative years. Underwriters created entirely new methods for assessing risks associated with steam engines, textile machinery, and chemical processes that had no historical precedent. These financial innovations proved essential for encouraging investment in unproven technologies that traditional risk assessment methods could not evaluate.
Specialized industrial insurance created systematic approaches to technology assessment and risk management that would accelerate technological adoption throughout the industrial period. These innovations reduced barriers to technological investment while providing systematic protection against the uncertainties inherent in industrial development.
Commodity exchanges
Finally, commodity exchanges established standardized trading practices for industrial raw materials that would support the systematic expansion of manufacturing operations. Cotton, wool, iron, and coal markets developed sophisticated pricing and delivery mechanisms that enabled manufacturers to plan production schedules and manage supply with a newfound accuracy and reliability.
Commodity exchanges created systematic raw material procurement and inventory management approaches to support industrial expansion across multiple sectors. These innovations in market organization and price discovery established foundations for systematic industrial planning that would influence manufacturing development throughout the Industrial Revolution and beyond.
Banking innovations extended beyond lending to encompass systematic approaches to payments, currency exchange, and international trade finance that would support industrial expansion across national boundaries. These developments created the financial infrastructure necessary for the global industrial economy that would emerge during subsequent periods of the technology cycle.
This comprehensive financial reorientation proved absolutely crucial because industrial development required capital investment patterns fundamentally different from those that had supported agricultural and commercial economies. The Core Formation Period’s final phase established the financial mechanisms and institutions that would enable the massive scaling of industrial operations during the Installation Period while creating sustainable foundations for long-term industrial growth.
Conclusion: The Foundation of Industrial Transformation
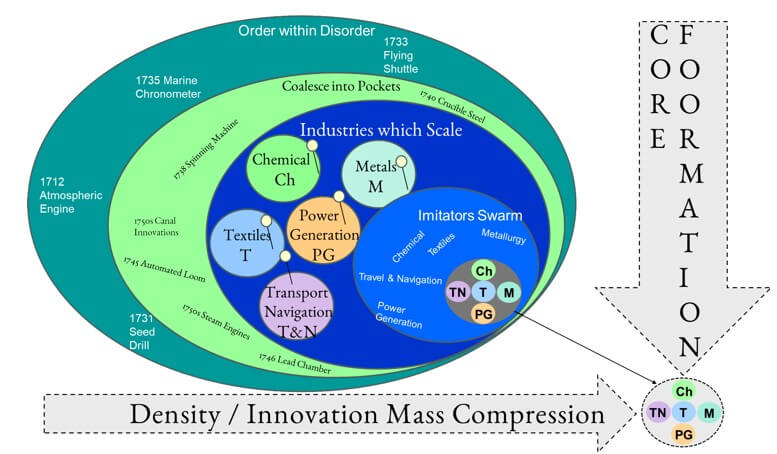
Arkwright’s Cromford Mill, pictured below
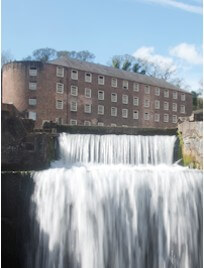
The chart above presents a visual perspective of the core formation process. It shows the sum of the five phases and how the technologies became incredibly dense. It follows Brian Arthur’s framework of technology evolution. Arthur proposed that technology evolves through ecosystems that build off one another. The technologies were often deployed in a way differing from the original design. The utilization of prior inventions can span decades and sometimes longer. The process is not linear. It is not dependent on any individual. Carlota Perez predicts this behavior through the core formation’s gestation period of her framework. Both frameworks work very well together in predicting these dynamics.
The Core Formation Period of the first technology cycle reveals the fundamentally systematic nature of what appeared to contemporaries as chaotic and unpredictable technological change. Rather than comprising a random collection of unrelated innovations scattered across time and sectors, the remarkable multi-decade gestation period followed predictable patterns that subsequent technology cycles would repeatedly demonstrate throughout the four technology cycles that followed.
Apparently unrelated but . . .
Initial ripples of apparently unrelated innovations gradually coalesced around systematic recognition of interconnected bottlenecks, leading to the emergence of revolutionary industries that competitive imitation and systematic improvement refined, all supported by comprehensive financial reorientation toward industrial ventures. The financial reorientation in phase five completed the gestation required for the innovations, enabling the core industries that would go on to power the Industrial Revolution. That will come in the Installation Period; however, the energy required to undergo this transformative process must be created first. The energy of the densely packed core of five industries would explode with the opening of the first automated cotton factory in Cromford Mill in 1771.
This demonstrates the Industrial Revolution did not begin in 1771 with the commencement of the Installation Period—it began four full decades earlier with the systematic development of technological and economic foundations that made subsequent industrial transformation possible. The Core Formation Period established not only the specific technologies that would power the first technology cycle but also the institutional frameworks, financial mechanisms, and industrial organization models that would define industrial capitalism for the next century.
Production organization
The Core Formation Period’s systematic development encompassed far more than technological innovation alone. It created comprehensive systems for organizing production, managing labor, financing expansion, and coordinating economic activity across multiple sectors and geographical regions. These systematic innovations proved just as crucial as specific technologies for enabling sustained industrial growth.
Furthermore, the Core Formation Period established systematic approaches to technology transfer and diffusion that would accelerate industrial development throughout subsequent phases. The period’s innovations in patent protection, licensing agreements, and technical support services created sustainable mechanisms for spreading technological knowledge while maintaining incentives for continued innovation.
Understanding this systematic pattern provides crucial insights for recognizing and navigating future technology cycles that follow similar developmental logic. The Core Formation Period demonstrates that major technological revolutions are not sudden disruptions that emerge without warning but systematic processes requiring decades of foundational development across multiple interconnected areas.
Beyond seemingly unrelated innovations
The Core Formation Period teaches us to look beyond individual innovations to identify systematic bottlenecks that require coordinated solutions. Contemporary observers who focus only on specific technologies miss the broader patterns of systematic development that determine whether innovations will achieve transformative impact or remain isolated improvements.
Moreover, the Core Formation Period demonstrates that technological revolution requires parallel innovations in financial systems, organizational structures, and institutional frameworks. Societies that fail to develop these supporting systems cannot realize the full potential of their technological innovations, regardless of their technical sophistication.
The legacy of the ~1730-1771 Core Formation Period extends far beyond the specific technologies it produced or even the industrial systems it established. It created the systematic approaches to innovation, organization, and economic development that would enable humanity to navigate subsequent technological revolutions successfully. The period established templates for how technological revolutions unfold and demonstrated that systematic innovation requires technical breakthroughs alongside institutional, financial, and organizational innovations.
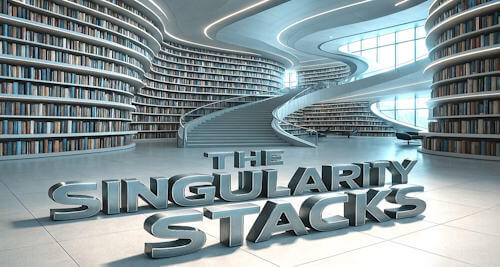
The reference library section lists the publications on the core formation for the first Perezian Period.
Link to the Gestation Periods Bibliography for the first technology cycle
Link to the Gestation Periods Innovations Listing for the first technology cycle
The next phase: The Installation irruption