
Cycle Two Core Formation Period 1800-1829
The Foundation for the Rail Revolution
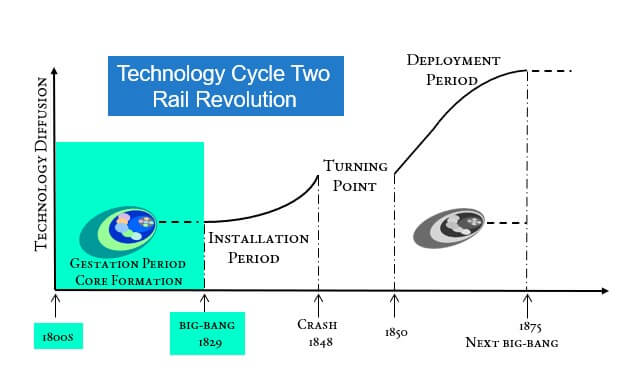
The second cycle core formation period was not a typical gestation period. Steam was already very well known. However, steam was re-imagined for use in mines for application in transportation. The Second Industrial Revolution proved to be the technology cycle that scaled industrialization, accelerating the speed of globalization.
The Core Formation Period between 1800 and 1830 marked a revolutionary transformation in human civilization. During these three decisive decades, five groundbreaking industries emerged that would fundamentally reshape society, economics, and technology. Steam power, railroads, chemicals, metallurgy, and machine tools evolved from experimental curiosities into commercial realities that powered an entirely new economic paradigm.
Moreover, this period demonstrates how technological revolutions unfold through distinct phases of development. Initially, unrelated innovations begin creating ripples across different sectors. Subsequently, these scattered developments coalesce around common problems and opportunities. Eventually, entirely new industries emerge while existing ones undergo complete transformation. Furthermore, widespread imitation and improvement accelerate technological diffusion. Finally, financial capital recognizes the commercial potential and redirects investment toward these industrial ventures.
The five industries that defined this Core Formation Period created interlocking networks of innovation and mutual reinforcement. Steam technology provided the power source that revolutionized transportation through railroads. Meanwhile, chemical advances enabled better metallurgical processes, which in turn produced superior materials for machine tools. Simultaneously, precision manufacturing techniques improved the reliability and efficiency of steam engines and railroad equipment. This essay examines how these five industries developed through the Core Formation Period’s five phases. Each phase reveals critical innovations, key figures, and transformative events that collectively established the foundation for the Steam and Railway Age. Additionally, the narrative demonstrates how seemingly isolated developments converged into a coherent technological revolution that would dominate the 19th century.
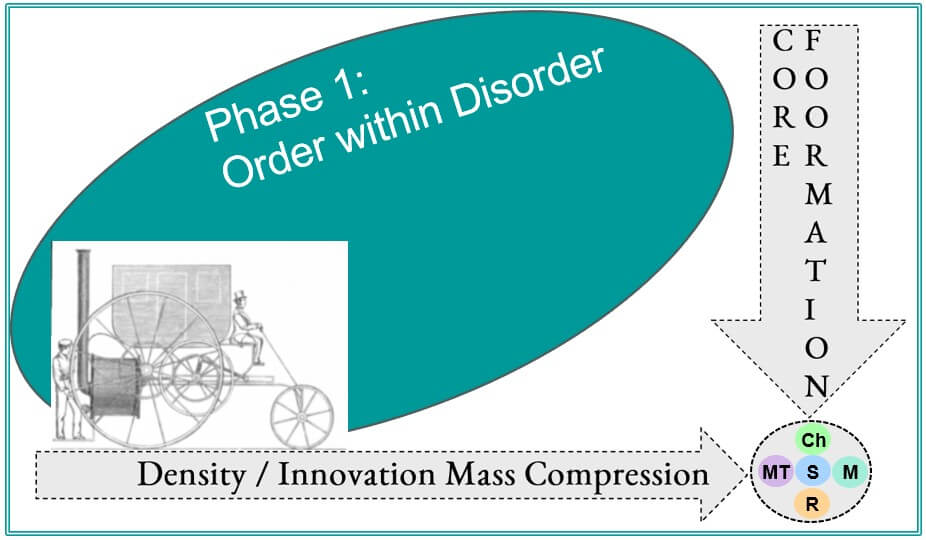
Phase 1: Initial Ripples (1800-1806)
Steam Power: Early Experimentation and Public Demonstration
The steam industry’s initial ripples began with dramatic public demonstrations that captured widespread attention. In 1803, Richard Trevithick built his steam-powered vehicle called the London Steam Carriage, which attracted considerable public and press attention when he drove it from Holborn to Paddington and back.
Trevithick’s is pictured on the left.
This spectacle demonstrated steam’s potential for transportation applications beyond traditional stationary engines.
Concurrently, Trevithick developed his high-pressure steam engine, which offered significant advantages over James Watt’s earlier low-pressure designs. His engines operated at pressures up to 50 pounds per square inch, compared to Watt’s engines that worked at atmospheric pressure. Consequently, Trevithick’s engines delivered more power while occupying less space, making them suitable for mobile applications.
Furthermore, Trevithick’s Penydarren locomotive made history in 1804 by becoming the first steam locomotive to run on rails. Although the locomotive successfully hauled ten tons of iron and seventy men over nine miles, the cast iron rails proved too brittle for the locomotive’s weight. Nevertheless, this demonstration proved that steam power could effectively move heavy loads along guided tracks.
Railroads: Tramway Networks and Early Track Systems
Railroad development during this phase focused primarily on expanding existing tramway networks used in mining operations. Numerous collieries throughout Britain employed horse-drawn wagons running on wooden rails to transport coal from mines to waterways. These systems demonstrated the efficiency of guided transportation for heavy materials.
Simultaneously, engineers experimented with different rail materials and configurations. Cast iron rails gradually replaced wooden ones because they offered greater durability and smoother surfaces. However, these early cast iron rails frequently broke under heavy loads, creating ongoing maintenance challenges for operators.
Additionally, the Surrey Iron Railway opened in 1803 as the first public railway authorized by Parliament. This horse-drawn system transported goods between Croydon and Wandsworth, establishing important precedents for future railroad development. The railway’s success demonstrated that guided transportation could serve commercial purposes beyond mining operations.
Chemicals: Alkali Production and Industrial Applications
The chemical industry’s initial ripples emerged from growing demand for alkali products in textile manufacturing. Nicolas Leblanc’s process for producing sodium carbonate from salt had revolutionized alkali production during the 1790s. By 1800, several British manufacturers had established works using this process to meet domestic demand.
Moreover, the Continental System imposed by Napoleon during the Napoleonic Wars created additional opportunities for British chemical manufacturers. European blockades disrupted traditional trade routes, forcing British manufacturers to develop domestic sources for essential chemicals. This situation accelerated innovation in chemical production processes.
Furthermore, early chemical manufacturers began exploring applications beyond traditional soap and glass production. They discovered that improved chemical processes could enhance textile dyeing, paper production, and food preservation. These applications demonstrated the chemical industry’s potential for transforming multiple sectors of the economy.
Metallurgy: Improved Iron Production and Quality Enhancement
Metallurgical innovations during this phase focused on improving iron production efficiency and quality. Henry Cort’s puddling process, developed in the 1780s, continued gaining adoption throughout British ironworks. This process produced wrought iron with superior properties compared to traditional methods, though it required significant skill and experience to master.
Additionally, ironmasters experimented with hot blast furnaces that promised substantial fuel savings. These furnaces preheated combustion air using waste heat from the furnace itself, improving thermal efficiency. Early trials suggested that hot blast could reduce coal consumption by up to 30%, making iron production more economical.
Meanwhile, regional iron producers developed specialized expertise in particular types of iron products. Sheffield manufacturers concentrated on high-quality steel production, while Welsh and Scottish ironworks focused on producing large quantities of basic iron for construction and manufacturing applications. This specialization improved overall industry efficiency.
Machine Tools and Precision Manufacturing: Workshop Innovation and Standardization
The machine tools industry’s initial ripples emerged from individual craftsmen’s innovations in their workshops. These artisans developed specialized tools and techniques to meet the growing demand for precision components required by steam engines and textile machinery. Their innovations laid the groundwork for systematic manufacturing processes.
Furthermore, early machine tool makers began standardizing their products and processes. They recognized that consistent measurements and interchangeable parts would improve manufacturing efficiency and reduce costs. This standardization effort required developing new measuring instruments and quality control procedures. Additionally, the concentration of skilled craftsmen in specific regions created knowledge-sharing networks that accelerated innovation. Manchester, Birmingham, and London emerged as centers of machine tool development, where craftsmen learned from each other and competed to develop superior techniques. These regional clusters fostered rapid technological advancement.
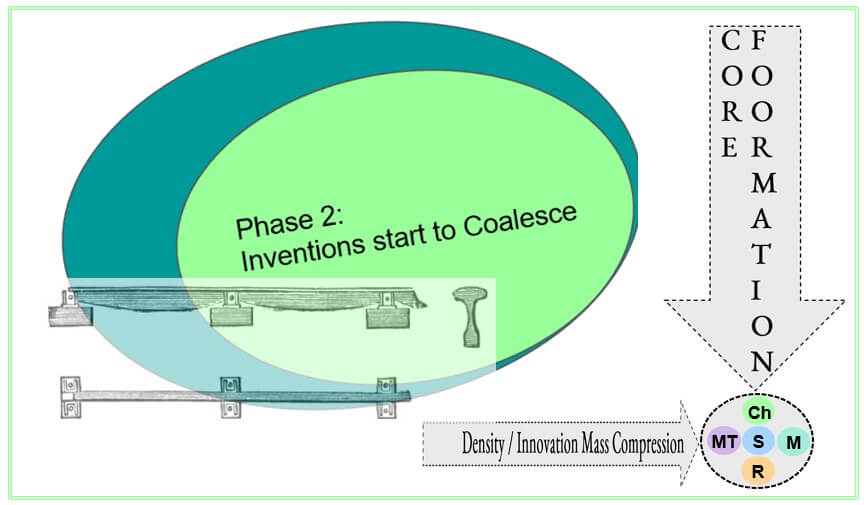
Phase 2: Coalescence (1806-1812)
Steam Power: Addressing Technical Bottlenecks and Commercial Viability
During the coalescence phase, steam technology developers focused on solving critical technical bottlenecks that limited commercial applications. Trevithick’s experiments with high-pressure steam engines revealed numerous engineering challenges that required systematic solutions.
Pictured on left, John Birkinshaw’s invention of wrought iron rails in 1820 was a critical response. It enabled longer-lasting rails that could better withstand the demands of steam locomotives, reduce maintenance needs, and improve operational safety.
Engineers also worked to improve boiler designs, valve mechanisms, and power transmission systems.
Notably, the development of better steam engine governors became crucial for reliable operation. These devices automatically regulated steam flow to maintain consistent engine speed under varying loads. Without effective governors, steam engines experienced dangerous speed fluctuations that could damage machinery or cause accidents.
Simultaneously, manufacturers began standardizing steam engine components to reduce production costs and improve reliability. They developed common specifications for cylinder bores, piston dimensions, and connecting rod lengths. This standardization enabled manufacturers to produce engines more efficiently while ensuring replacement parts would fit properly.
Railroads: Infrastructure Development and Load-Bearing Solutions
Railroad development during this phase addressed fundamental infrastructure challenges that limited system expansion. The brittleness of cast iron rails created ongoing problems for operators, who frequently faced expensive repairs and service disruptions. Engineers recognized that stronger rail materials were essential for supporting heavier loads and more frequent traffic.
Consequently, several inventors experimented with different rail designs and materials. They tested various cross-sectional shapes to distribute loads more effectively and explored different iron alloys to improve durability. These experiments laid the groundwork for future innovations in rail technology. Moreover, railroad builders developed improved track-laying techniques that provided better support for rails and reduced maintenance requirements. They experimented with different types of sleepers, ballast materials, and drainage systems. These infrastructure improvements proved essential for creating reliable railroad networks.
Chemicals: Process Optimization and Market Expansion
The chemical industry’s coalescence phase focused on optimizing existing processes and expanding into new markets. Manufacturers refined the Leblanc process to reduce waste, improve yields, and lower production costs. They developed better furnace designs, improved raw material handling, and enhanced product purification techniques.
Additionally, chemical manufacturers began integrating their operations to capture value from byproducts and waste materials. They discovered that substances previously discarded could serve as raw materials for other chemical processes. This integration reduced costs while creating new revenue streams.
Furthermore, the growing textile industry created increasing demand for chemical products beyond traditional alkali. Manufacturers developed new dyestuffs, bleaching agents, and textile treatments that improved product quality and reduced processing time. These innovations demonstrated the chemical industry’s potential for supporting industrial growth.
Metallurgy: Fuel Efficiency and Production Scaling
Metallurgical development during this phase concentrated on improving fuel efficiency and scaling production to meet growing demand. The hot blast furnace technology developed by James Beaumont Neilson in 1806 began attracting serious attention from ironmasters seeking to reduce coal consumption and improve profitability.
Simultaneously, iron producers worked to standardize their products and improve quality control. They developed better testing methods to ensure consistent iron properties and established quality grades for different applications. This standardization helped customers select appropriate materials for specific uses. Moreover, regional specialization continued developing as different areas focused on particular types of iron products. This specialization allowed producers to optimize their equipment and processes for specific applications, improving efficiency and product quality. The resulting network of specialized producers created a more robust and efficient industry.
Machine Tools and Precision Manufacturing: Systematic Approaches and Knowledge Transfer
The machine tools industry’s coalescence phase emphasized systematic approaches to manufacturing and knowledge transfer between craftsmen. Skilled artisans began documenting their techniques and developing training programs for apprentices. This knowledge codification accelerated skill development and improved manufacturing consistency.
Additionally, machine tool makers started collaborating with steam engine manufacturers to develop specialized equipment for engine production. They created boring machines for cylinders, lathes for turning shafts, and precision measuring instruments for quality control. These collaborations improved both industries’ capabilities.
Furthermore, the establishment of technical societies and publications facilitated knowledge sharing among craftsmen and engineers. These organizations provided forums for discussing innovations, sharing experiences, and coordinating standardization efforts. Such knowledge networks proved essential for accelerating technological development.
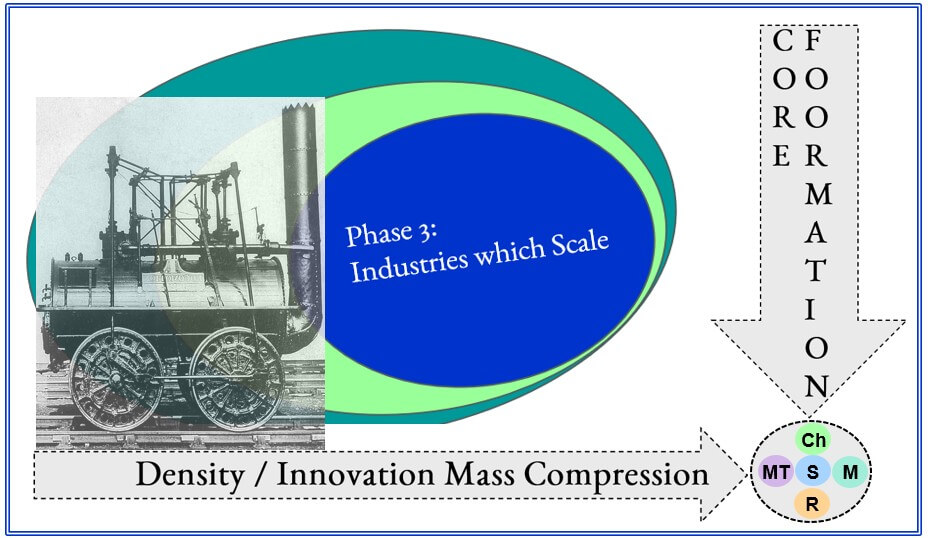
Phase 3: Emergence of New and Revolutionized Industries (1812-1818)
Steam Power: Commercial Applications and Market Recognition
The emergence phase witnessed steam power’s transformation from experimental technology to commercially viable industrial solution. Steam engines began powering textile mills, flour mills, and other manufacturing facilities throughout Britain.
Pictured on the left was a locomotive designed between 1818 and 1821 by George Stephenson. He played a critical role in establishing the foundation of the rail industry through his involvement with the Stockton and Darlington Railway
These applications demonstrated steam’s reliability and economic advantages over traditional water power.
Concurrently, steam engine manufacturers established systematic production processes that reduced costs and improved quality. They developed specialized workshops, trained skilled workers, and standardized component designs. These improvements made steam engines more accessible to a broader range of customers.
Furthermore, the marine steam engine market began developing as inventors adapted land-based engines for shipboard use. Although early steamships faced technical challenges and skepticism from traditional mariners, successful demonstrations proved that steam could revolutionize water transportation. This market expansion provided new growth opportunities for steam engine manufacturers.
Railroads: Systematic Development and Engineering Solutions
Railroad development during this phase focused on systematic engineering approaches that addressed infrastructure challenges and operational requirements. Engineers developed comprehensive solutions for track construction, including improved rail designs, better foundation systems, and standardized construction techniques.
Importantly, the development of more durable rails became a priority as railroad traffic increased. Engineers experimented with different rail profiles and materials to create stronger, longer-lasting track systems. They also developed better joining methods to create smooth, continuous rail surfaces that reduced wear and improved ride quality.
Additionally, railroad operators began developing systematic approaches to traffic management and scheduling. They created timetables, established stations, and developed signaling systems to coordinate train movements. These operational innovations proved essential for safe and efficient railroad operations.
Chemicals: Industrial Integration and Product Diversification
The chemical industry’s emergence phase featured increasing integration with other industrial sectors and significant product diversification. Chemical manufacturers expanded beyond traditional alkali production to serve growing markets in textiles, paper, soap, and food processing. This diversification reduced dependence on single markets and improved profitability.
Moreover, manufacturers began developing specialized chemical products for specific industrial applications. They created improved dyestuffs for textile manufacturers, better bleaching agents for paper producers, and specialized chemicals for metallurgical processes. This specialization allowed manufacturers to command premium prices for superior products.
Simultaneously, chemical manufacturers invested in research and development to improve existing processes and develop new products. They established laboratories, hired trained chemists, and systematically investigated chemical reactions and processes. This research orientation distinguished the chemical industry from traditional craft-based manufacturing.
Metallurgy: Technical Innovation and Market Expansion
Metallurgical development during this phase emphasized technical innovation and market expansion to meet growing industrial demand. Iron producers adopted new technologies like hot blast furnaces that significantly reduced fuel consumption while improving iron quality. These innovations made iron production more economical and environmentally sustainable.
Additionally, ironmasters began producing specialized iron products for specific applications. They developed different grades of iron for construction, machinery, and transportation uses. This product specialization allowed producers to optimize their processes and command premium prices for superior materials.
Furthermore, the growing railroad and steam engine markets created unprecedented demand for high-quality iron products. Metallurgical producers responded by expanding capacity and improving quality control systems. They developed new testing methods and quality standards to ensure their products met customer requirements.
Machine Tools and Precision Manufacturing: Technological Advancement and Industry Formation
The machine tools industry’s emergence phase featured rapid technological advancement and the formation of a distinct industrial sector. Machine tool makers developed increasingly sophisticated equipment that improved manufacturing precision and productivity. These innovations enabled the production of complex machinery with previously unattainable accuracy.
Notably, manufacturers began producing complete machine tool systems rather than individual tools. They integrated multiple operations into single machines and developed automated feeding and control systems. These integrated systems improved manufacturing efficiency while reducing labor requirements.
Moreover, the establishment of specialized machine tool manufacturers created a distinct industry focused on serving other manufacturing sectors. These companies developed expertise in precision manufacturing techniques and invested in research and development to improve their products. This specialization accelerated technological advancement throughout the manufacturing economy.
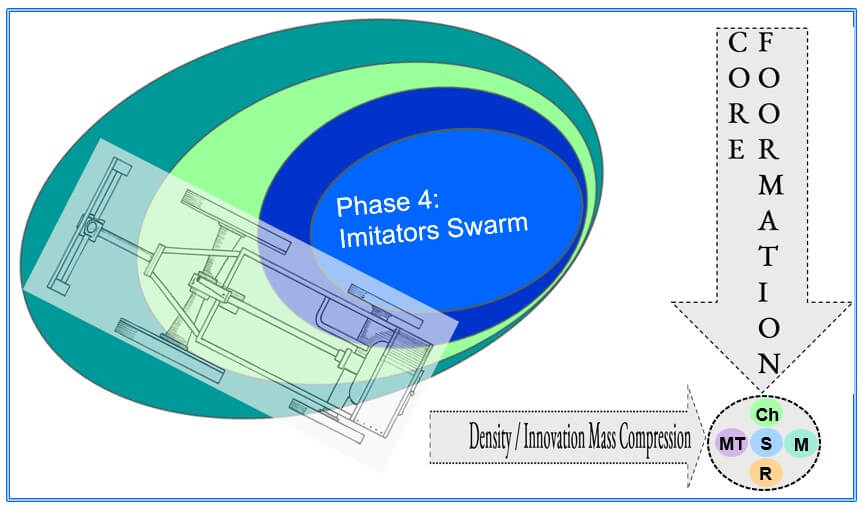
Phase 4: Imitation and Improvement (1818-1824)
Steam Power: Widespread Adoption and Technological Refinement
The imitation and improvement phase witnessed widespread adoption of steam technology across multiple industries and regions. Manufacturers throughout Britain and Europe began installing steam engines in their facilities, driven by proven economic benefits and improved reliability.
Pictured on the left is drawing of Timothy Hackworth’s innovations. It incorporated several key innovations, including: Inverted vertical cylinders with direct drive to the wheels. An aligned steam blastpipe, which uses exhaust steam to improve the draft through the fire and increase steam production and power.
This adoption created a substantial market for steam engine manufacturers.
Simultaneously, numerous inventors and engineers worked to improve steam engine designs and performance. They developed more efficient boilers, better valve systems, and improved power transmission mechanisms. These incremental improvements collectively enhanced steam engine reliability and reduced operating costs.
Furthermore, regional manufacturers began adapting steam engine designs to local conditions and requirements. They modified engines for different fuels, climates, and applications. This adaptation process resulted in diverse steam engine designs optimized for specific markets and uses.
Railroads: Network Expansion and Operational Innovation
Railroad development during this phase focused on network expansion and operational innovation as the technology’s commercial viability became apparent. Multiple railroad projects began throughout Britain, creating competition among routes and driving technological improvements. This competition accelerated innovation and reduced transportation costs.
Importantly, the Stockton and Darlington Railway project gained momentum during this period. Between 1818 and 1821, George Stephenson played a crucial role in establishing the foundation of the rail industry through his involvement with this pioneering railroad. He was appointed engineer for the railway’s construction in 1821.
Initially, Edward Pease, the railway’s main promoter, intended for the line to use horse-drawn carriages. However, Stephenson, who had built successful steam locomotives for coal hauling at Killingworth Colliery, convinced Pease of the benefits of steam power. He argued that a steam engine could pull significantly more weight and travel faster than horses.
The original plan faced resistance, particularly from landowners concerned about the railway’s impact. A revised bill, incorporating Stephenson’s proposed route deviations and the use of “loco-motives or moveable engines,” received royal assent on May 23, 1823. This approval marked a crucial milestone in railroad development.
Additionally, in 1823, Stephenson and Pease established Robert Stephenson and Company, a locomotive factory in Newcastle. They anticipated growing demand for locomotives and railway development. This company built the first locomotive for the Stockton and Darlington Railway, named Locomotion No. 1.
Chemicals: Process Refinement and Quality Improvement
The chemical industry’s imitation and improvement phase featured systematic process refinement and quality improvement initiatives. Manufacturers adopted best practices from successful operations and adapted them to their specific circumstances. This knowledge transfer accelerated industry-wide improvements in efficiency and product quality.
Moreover, manufacturers invested in improving production processes to reduce costs and enhance product consistency. They developed better mixing techniques, improved heating systems, and enhanced purification methods. These improvements made chemical products more reliable and cost-effective for industrial customers.
Furthermore, the growing competition among chemical manufacturers drove innovation in product development and customer service. Companies developed specialized products for specific applications and provided technical support to help customers optimize their processes. This customer-focused approach differentiated successful companies from their competitors.
Metallurgy: Production Optimization and Quality Standards
Metallurgical development during this phase emphasized production optimization and the establishment of quality standards that would support industrial growth. Iron producers refined their processes to improve consistency and reduce waste. They developed better furnace designs, improved raw material handling, and enhanced quality control procedures.
Additionally, the introduction of John Birkinshaw’s wrought iron rails in 1820 represented a critical response to the railroad industry’s needs. Due to the weight of heavy locomotives, these rails provided a crucial solution. They enabled longer-lasting rails that could better withstand the demands of steam locomotives, reduce maintenance needs, and improve operational safety.
Simultaneously, iron producers began establishing quality standards and testing procedures to ensure their products met customer requirements. They developed standardized testing methods and quality grades for different applications. These standards helped customers select appropriate materials and reduced the risk of product failures.
Machine Tools and Precision Manufacturing: Standardization and Efficiency Improvements
The machine tools industry’s imitation and improvement phase focused on standardization and efficiency improvements that would support broader industrial development. Manufacturers adopted successful techniques from leading companies and adapted them to their operations. This knowledge transfer accelerated industry-wide improvements in productivity and quality.
Moreover, machine tool makers worked to standardize component designs and manufacturing processes. They developed common specifications for cutting tools, measuring instruments, and machine components. This standardization reduced costs and improved interchangeability of parts and tools.
Furthermore, manufacturers invested in developing more efficient production methods and improved workshop organization. They implemented systematic approaches to workflow, inventory management, and quality control. These improvements enhanced productivity while reducing manufacturing costs and delivery times.
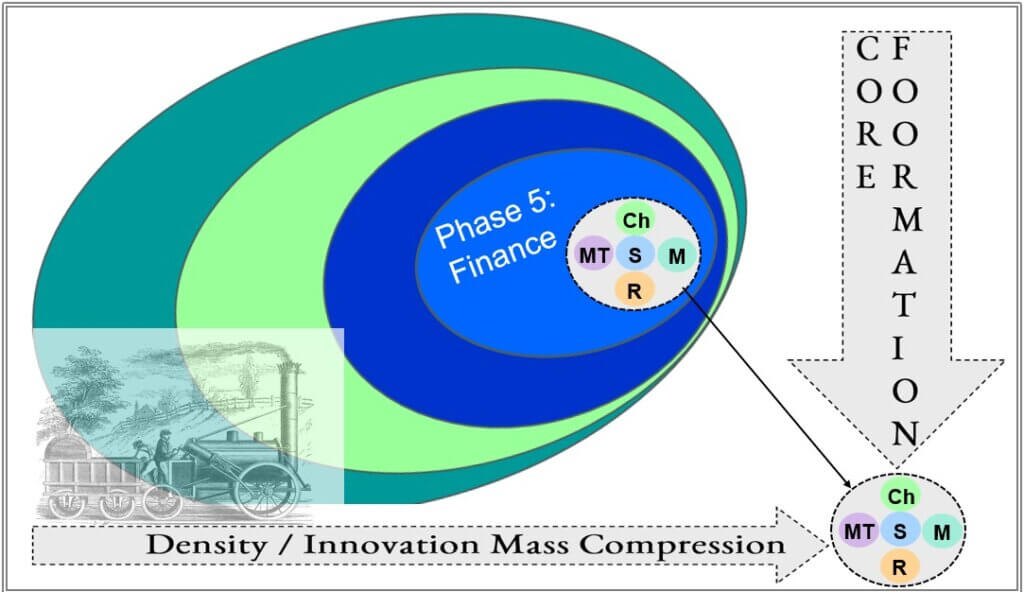
Phase 5: Financial Reorientation Toward Industrial Ventures (1824-1830)
Steam Power: Capital Investment and Market Maturation
The financial reorientation phase witnessed significant capital investment in steam power development and market maturation. Investors recognized steam technology’s commercial potential and directed substantial resources toward steam engine manufacturing and applications.
Pictured on the left is an early train on the Liverpool and Manchester Railway, which opened in 1830. It was the first modern, inter-city passenger railway, the first to rely exclusively on steam power.
This investment put the final pieces in place for the development of core densities. After phase five, the core was ready to launch the second technology cycle.
Consequently, steam engine manufacturers expanded their operations and invested in improved production facilities. They built larger factories, acquired specialized equipment, and hired skilled workers. These investments enabled manufacturers to meet growing demand while reducing production costs through economies of scale.
Furthermore, steam power applications expanded into new markets as investors funded innovative projects. Steam engines began powering printing presses, food processing equipment, and mining machinery. This market diversification reduced dependence on traditional applications and created new growth opportunities.
Railroads: Investment Mobilization and Infrastructure Development
Railroad development during this phase featured unprecedented investment mobilization and systematic infrastructure development. The Liverpool and Manchester Railway project attracted substantial investment during this period, demonstrating systematic approaches to railway financing that could mobilize capital for major infrastructure development.
Importantly, the project’s success established templates for railway investment that would characterize massive railway expansion throughout subsequent decades. These investment patterns proved that railway development could achieve commercial viability while transforming transportation systems. Investors gained confidence in railroad technology’s potential for generating substantial returns. Moreover, the financial success of early railroad projects attracted additional capital from both domestic and international sources. Investors recognized that railroads could generate revenue through passenger fares, freight charges, and land development opportunities. This recognition led to numerous railroad projects throughout Britain and Europe.
Chemicals: Capital Accumulation and Industrial Expansion
The chemical industry’s financial reorientation phase featured significant capital accumulation and industrial expansion as investors recognized the sector’s growth potential. Chemical manufacturers attracted investment for expanding production capacity and developing new products. This capital injection accelerated industry growth and technological advancement.
Additionally, investors funded research and development initiatives that improved chemical processes and product quality. They established laboratories, hired skilled chemists, and supported systematic investigation of chemical reactions and applications. These investments differentiated the chemical industry from traditional manufacturing sectors. Furthermore, the integration of chemical operations with other industrial sectors attracted investment in comprehensive industrial complexes. Investors funded facilities that combined chemical production with textile manufacturing, paper production, and other applications. These integrated operations improved efficiency and profitability.
Metallurgy: Investment in Advanced Technology and Capacity Expansion
Metallurgical development during this phase emphasized investment in advanced technology and capacity expansion to meet growing industrial demand. Investors funded the construction of modern iron works equipped with hot blast furnaces and improved production systems. These investments significantly increased production capacity and efficiency.
Moreover, the success of Timothy Hackworth’s Royal George locomotive in 1827 demonstrated the importance of high-quality metallurgical products for railroad development. Built in 1827, the locomotive addressed shortcomings of earlier designs and incorporated several key innovations, including inverted vertical cylinders with direct drive to the wheels.
The Royal George became the first locomotive with three axles coupled by outside coupling rods, making it the ancestor of the 0-6-0 British goods engines. Additionally, it featured a correctly aligned steam blastpipe, which used exhaust steam to improve the draught through the fire and increase steam production and power.
The Royal George proved reliable in service and with its six coupled wheels provided stability for pulling heavy loads in all weather conditions. It served the Stockton and Darlington Railway well for almost two decades, demonstrating the potential of steam locomotives for heavy mineral haulage. The success of the Royal George contributed significantly to locomotive technology advancement and paved the way for future developments in railway engineering.
Machine Tools and Precision Manufacturing: Investment in Innovation and Market Development
The machine tools industry’s financial reorientation phase featured substantial investment in innovation and market development that established the foundation for modern manufacturing. Investors recognized that precision manufacturing capabilities were essential for supporting the growing steam and railroad industries.
Consequently, machine tool manufacturers attracted capital for developing advanced manufacturing equipment and expanding production capabilities. They invested in precision measuring instruments, improved cutting tools, and automated production systems. These investments enhanced manufacturing accuracy and productivity.
Furthermore, investors funded the establishment of specialized machine tool companies that focused on serving specific industrial sectors. These companies developed expertise in particular applications and invested in research and development to improve their products. This specialization accelerated technological advancement throughout the manufacturing economy.
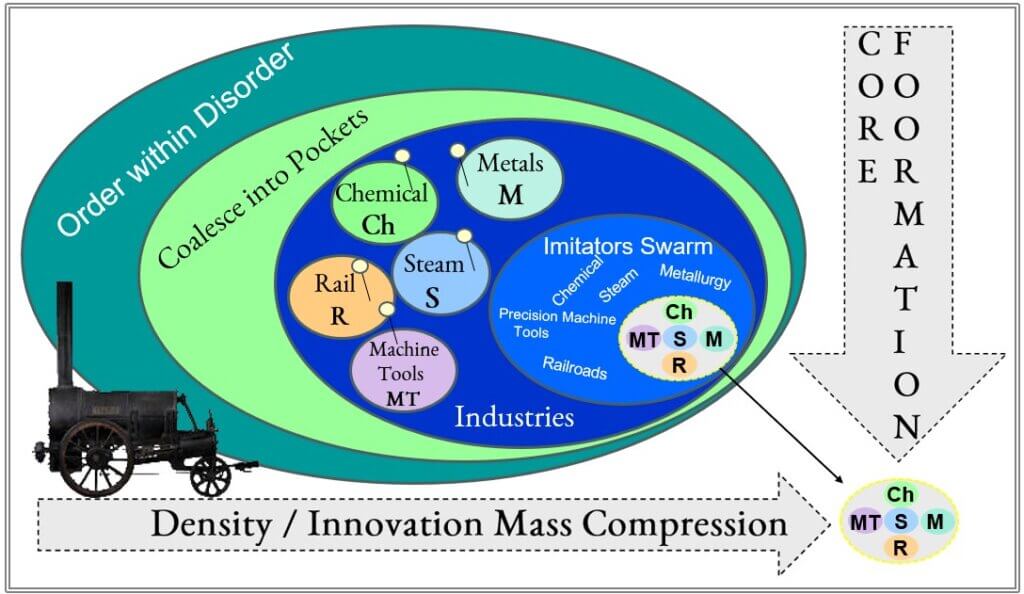
Conclusion
The Core Formation Period between 1800 and 1830 established the technological and economic foundation for the Steam and Railway Age that would dominate the 19th century.
Through five distinct phases of development, steam power, railroads, chemicals, metallurgy, and machine tools evolved from experimental technologies into commercially viable industries that transformed the world.
Pictured on the left is Stephenson’s Rocket. The engine was designed for the Liverpool and Manchester Railway and proved decisive enough to become the Big Bang flash point for the launch of the Second Industrial Revolution.
The initial ripples phase demonstrated that isolated innovations could capture public attention and prove technical feasibility. Subsequently, the coalescence phase showed how these innovations could address common bottlenecks and create mutual reinforcement. The emergence phase proved that new industries could achieve commercial viability and market acceptance.
Moreover, the imitation and improvement phase revealed how widespread adoption could accelerate technological refinement and cost reduction. Finally, the financial reorientation phase demonstrated that capital markets could recognize and support industrial transformation on an unprecedented scale.
The interlocking nature of these five industries created powerful synergies that accelerated technological development and economic growth. Steam power provided the energy source for railroad transportation and industrial machinery. Railroads created demand for improved metallurgical products and precision manufacturing. Chemical advances supported better metallurgical processes and industrial applications.
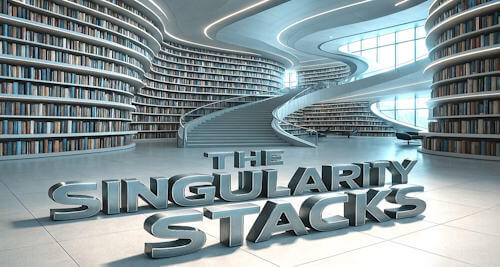
The innovations reference library section lists the inventions from the Perezian Periods in which they occurred for the second technology cycle. The link is below:
The Publications and Innovations Library for the entire Second Technology Cycle.
The main entrance to Technology Cycles Main Library – The Singularity Stacks Link
The picture of the Stacks is a hotlink as well