Core Formation Cycle Three

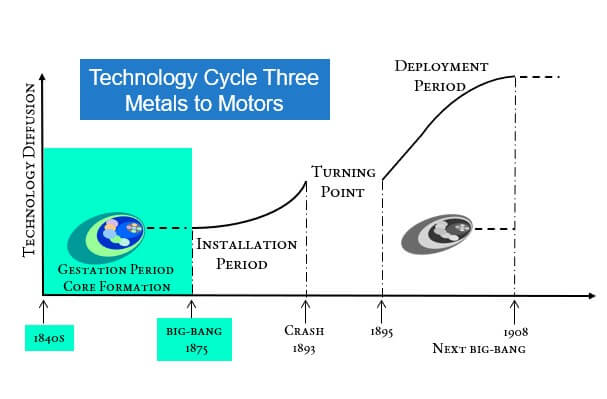
The Core Formation Period of the Third Technology Cycle (1840-1870s):
The Core Formation Period of the Steel & Electrical Age represents the crucial foundational phase that built upon existing railway and steam infrastructure. Between 1840 and 1870, a remarkable transformation unfolded across six interconnected industries. This thirty-year gestation period established the technological and economic foundations for Steel, Electricity, Heavy Manufacturing & Machinery, Railroads, Chemicals, and Telecommunications.
Moreover, this period demonstrates how seemingly unrelated innovations gradually converged into a coherent technological paradigm. The Core Formation Period created the essential infrastructure and industrial capabilities that would define the late nineteenth century’s massive expansion. Understanding this phase reveals how modern industrial civilization emerged from scattered experiments into systematic industrial development.
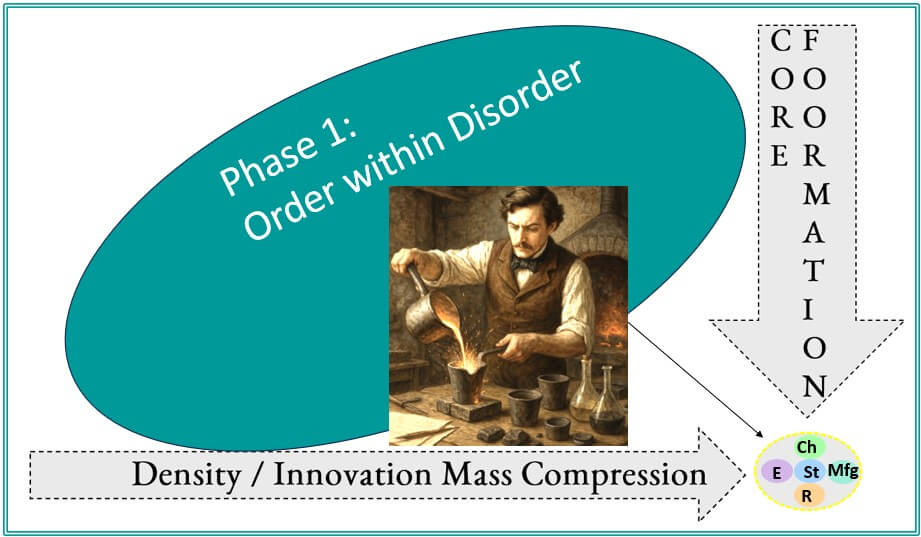
Phase 1: Initial Ripples 1840-1850
Seemingly Unrelated Innovations
During the 1840s, inventors and entrepreneurs pursued independent innovations across multiple fields without recognizing their future interconnections.
Pictured on the left is an AI-created image of Henry Bessemer working on early iron purification experiments 1840-1845.
These scattered developments would later prove essential to the emergence of the Steel and Electrical technology cycle.
Steel Industry Foundations
Henry Bessemer began his groundbreaking experiments with iron purification during the 1840s. His early work focused on removing impurities from molten iron through systematic air injection. Although Bessemer faced numerous technical challenges, his persistence laid the groundwork for revolutionary steel production methods. These initial experiments attracted little attention from established iron works, which remained satisfied with traditional wrought iron production.
Simultaneously, other metallurgists explored different approaches to iron improvement. Robert Mushet developed techniques for adding carbon and manganese to molten iron. His experiments complemented Bessemer’s work, though neither inventor initially recognized their mutual contributions. The iron industry continued relying on charcoal-based production methods that limited output and quality.
Electrical Innovations
Humphry Davy’s electric arc lighting demonstrations captivated audiences throughout the 1840s. His powerful electric arcs illuminated public spaces with unprecedented brilliance. However, these demonstrations required enormous batteries and consumed materials rapidly. Davy’s work inspired other researchers to explore electricity’s practical applications beyond laboratory curiosities.
Furthermore, Michael Faraday’s electromagnetic induction principles gained recognition among scientific communities. His discoveries revealed electricity’s potential for mechanical power generation. Nevertheless, practical applications remained limited by battery technology and electrical component manufacturing capabilities. Scientists continued viewing electricity primarily as a fascinating natural phenomenon rather than an industrial tool.
Heavy Manufacturing Developments
James Nasmyth designed his revolutionary steam hammer concept in 1839, addressing the limitations of existing forging equipment. His design promised to forge massive iron components with unprecedented precision and power. Traditional hammers required extensive manual labor and produced inconsistent results for large-scale metalworking projects.
Additionally, precision tool making began attracting serious industrial attention. Joseph Whitworth started developing systematic approaches to machine tool accuracy during this period. His early work established principles for standardized measurements and improved manufacturing consistency. These innovations would prove crucial for the heavy machinery industry’s future development.
Railroad Expansion Planning
Railway companies launched systematic route surveying projects across continental distances during the 1840s. Engineers developed sophisticated techniques for evaluating geographic obstacles and calculating construction costs. These surveys revealed the enormous scope of infrastructure development required for truly national transportation networks.
Concurrently, railroad construction techniques evolved to handle challenging terrain and longer distances. Engineers experimented with different bridge designs and earthwork methods. The Baltimore and Ohio Railroad pioneered several construction innovations that other companies quickly adopted. These advances prepared the industry for the massive expansion projects that would characterize later decades.
Chemical Industry Origins
August Wilhelm von Hofmann’s coal tar chemistry discoveries in 1845 opened entirely new possibilities for organic chemical production. His systematic analysis of coal byproducts revealed numerous valuable compounds previously unknown to science. Traditional chemistry focused primarily on inorganic materials and basic metal extraction processes.
Moreover, industrial demand for chemicals began exceeding traditional production methods’ capabilities. Textile manufacturers required consistent dye supplies and bleaching agents. Metalworking industries needed reliable acids and cleaning solutions. These growing demands encouraged chemists to explore systematic production methods for organic compounds.
Telecommunications Breakthrough
Samuel Morse’s Baltimore-Washington telegraph line commenced commercial operations in 1844, demonstrating electricity’s communication potential. His system transmitted messages across 40 miles instantaneously, revolutionizing long-distance communication. Previously, information traveled no faster than horses or sailing ships could carry written messages. Subsequently, telegraph companies recognized the enormous commercial potential of electrical communication networks. Entrepreneurs began planning telegraph lines connecting major commercial centers. The success of Morse’s initial line attracted significant investment capital for network expansion.
These early developments established telecommunications as a future commercial industry.
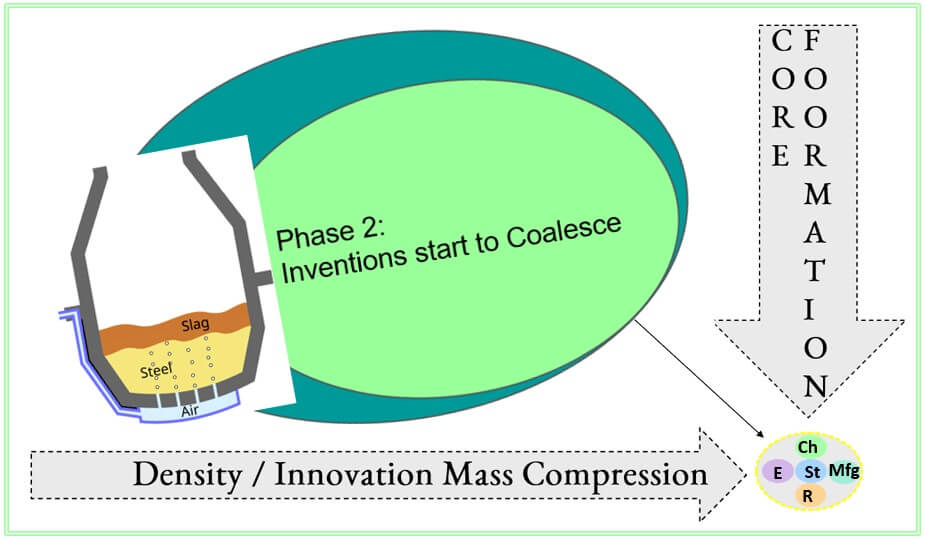
Phase 2: Coalescence to Solve Bottlenecks (~1850-1855)
Conversion laboratory process to industrial production
By 1850, the limitations of existing steam-age infrastructure became increasingly apparent. Growing industrial demands exposed critical bottlenecks that required systematic solutions across multiple related industries.
Pictured on the left is a drawing of the commercial Bessemer steel prototype testing process (1851-1855) is shown on the left. This process solved quality control and scaling problems, preventing the core new industry’s emergence.
The structural limitations became increasingly problematic for large-scale projects, which is why the second phase of the core formation period became so important.
Wrought iron’s structural limitations became increasingly problematic for large-scale construction projects. Traditional iron lacked the strength and consistency required for massive bridges and heavy machinery components. Railroad companies discovered that iron rails wore out rapidly under increasing train weights and traffic volumes.
Furthermore, the construction industry demanded stronger materials for taller buildings and longer bridge spans. Existing iron production methods could not deliver the quality and quantity required for ambitious architectural projects. Engineers recognized that breakthrough innovations in metallurgy would determine future construction possibilities.
Electrical Power Generation Challenges
The telegraph’s commercial success revealed electricity’s broader potential for power generation and distribution. However, battery technology remained expensive and impractical for large-scale applications. Industrial facilities required reliable power sources that could operate continuously without constant battery replacement.
Additionally, electrical component manufacturing faced significant technical challenges. Consistent wire production, reliable insulation materials, and durable electrical connections required systematic industrial development. Existing craftwork methods could not produce electrical components with the precision and reliability that emerging applications demanded.
Heavy Manufacturing Capacity Constraints
Existing machine tools proved insufficient for the precision manufacturing requirements of emerging technologies. Steam engines, railroad components, and precision instruments demanded manufacturing capabilities beyond traditional blacksmith and craftwork methods. Industrial facilities needed systematic approaches to producing identical components with consistent specifications.
Moreover, the scale of manufacturing projects exceeded traditional workshop capabilities. Large steam engines and railroad locomotives required integrated manufacturing facilities with specialized equipment. Traditional craftwork could not deliver the volume and consistency that expanding industries required.
Railroad Infrastructure Limitations
Iron rails and wooden bridges reached their structural limits as trains became heavier and more frequent. Traditional railroad construction methods could not support the traffic volumes that profitable operations required. Existing infrastructure frequently required expensive repairs and replacements that undermined railroad profitability.
Concurrently, railroad companies recognized that continental networks required systematic engineering approaches beyond traditional construction methods. The enormous scale of transcontinental projects demanded new construction techniques, materials, and organizational systems. Successful completion of these projects would require unprecedented coordination between multiple industries.
Chemical Processing Inadequacies
Industrial demand for systematic chemical production exceeded traditional methods’ capabilities. Textile manufacturers needed consistent dye supplies that natural materials could not provide reliably. Metalworking industries required standardized acids and cleaning solutions for systematic production processes.
Furthermore, traditional chemical production relied on natural materials with seasonal availability and quality variations. Industrial applications demanded consistent chemical supplies with reliable specifications. Systematic chemical production would require new manufacturing methods and quality control systems.
Telecommunications Network Requirements
Point-to-point telegraph lines provided valuable service, but systematic network expansion required significant technical innovations. Multiple telegraph lines sharing routes needed improved insulation and signal management systems. Existing technology could not support the complex networks that national communication systems required.
Additionally, message handling and routing systems became increasingly complex as networks expanded. Telegraph operators needed systematic methods for managing multiple simultaneous messages across interconnected routes. Network reliability required standardized equipment and operational procedures that individual operators could not develop independently.
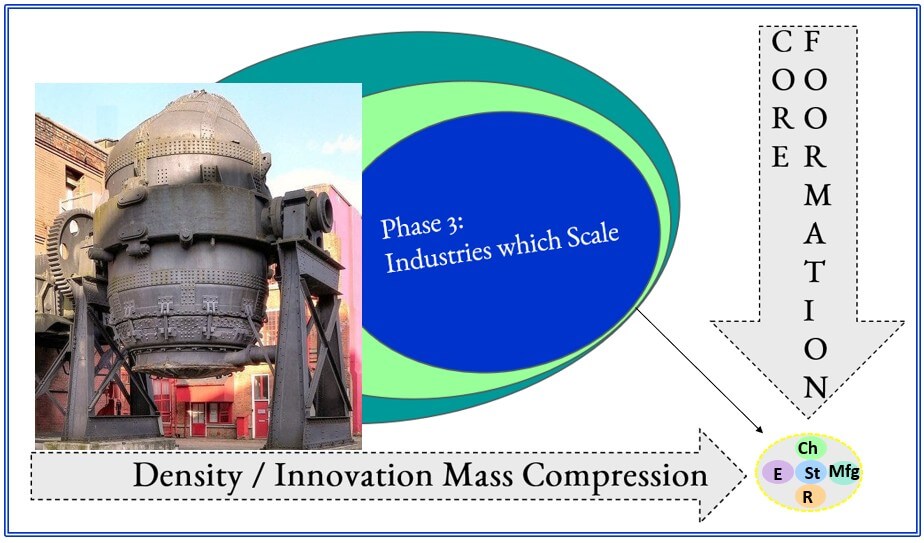
Phase 3: Emergence of New & Revolutionized Industries
1855 – 1865
Between 1855 and 1865, the scattered innovations of previous decades coalesced into systematic industry formation.
Bessemer Commercial Steel Production at Sheffield (1856) is pictured on the left. It was the first systematic mass production of steel at 10 tons daily
Entrepreneurs and engineers developed integrated approaches that transformed experimental technologies into profitable commercial enterprises.
Steel Industry Revolution
The Bessemer Steel process achieved commercial implementation in 1856, revolutionizing metalworking industries worldwide. Bessemer’s converter removed impurities from molten iron through controlled air injection, producing high-quality steel at unprecedented speeds. His process reduced steel production costs dramatically while improving material consistency and strength.
Additionally, steel production facilities required significant capital investment and systematic operational procedures. The Bessemer process demanded precise temperature control, timing, and material handling that traditional ironworks could not provide. Successful steel companies developed integrated operations that controlled every aspect of production from raw materials to finished products.
Electrical Power Generation
Faraday’s electromagnetic induction principles found practical application in dynamo electric generators during the 1860s. These devices converted mechanical energy into electrical power with efficiency that battery systems could not match. Industrial facilities gained access to reliable electrical power for lighting, communications, and mechanical applications.
Moreover, electrical generator manufacturing became a specialized industry requiring precision metalworking and systematic quality control. Generator components demanded exact specifications and consistent materials that traditional craftwork could not deliver. Successful electrical equipment manufacturers developed integrated production systems that ensured reliable performance under demanding industrial conditions.
Heavy Manufacturing & Machinery Transformation
Joseph Whitworth’s precision machine tools revolutionized manufacturing capabilities during the 1860s. His systematic approach to accuracy and standardization enabled consistent production of identical components. Manufacturing facilities could produce complex machinery with interchangeable parts and reliable specifications.
Furthermore, heavy machinery manufacturing required integrated facilities that combined multiple specialized capabilities. Steam engine production demanded precision boring, accurate casting, and systematic assembly procedures. Successful machinery manufacturers developed comprehensive production systems that coordinated numerous specialized operations.
Railroad Construction Acceleration
The Pacific Railway Act of 1862 launched systematic transcontinental railroad construction that demonstrated advanced engineering and organizational capabilities. Construction companies developed specialized equipment and procedures for rapid track laying across challenging terrain. These projects required unprecedented coordination between multiple contractors, suppliers, and government agencies.
Simultaneously, railroad construction techniques evolved to handle massive earthwork projects and complex bridge construction. Engineers developed systematic approaches to route selection, gradient calculation, and materials management. Successful railroad construction required integrated planning that coordinated engineering, procurement, and construction activities across continental distances.
Revolutionizing the Chemical Industry
William Henry Perkin’s mauve discovery in 1856 launched the synthetic dye industry and demonstrated organic chemistry’s commercial potential. His systematic approach to chemical synthesis opened possibilities for numerous industrial applications beyond traditional natural materials. Chemical manufacturers developed integrated production systems that controlled every aspect of synthesis from raw materials to finished products.
Additionally, industrial chemistry required systematic quality control and standardization that traditional methods could not provide. Chemical applications in textiles, metalworking, and manufacturing demanded consistent specifications and reliable supplies. Successful chemical companies developed integrated operations that ensured product consistency and supply reliability.
Telecommunications Network Development
Cyrus Field’s transatlantic telegraph cable projects of 1858 and 1866 demonstrated systematic approaches to international communication networks. His organization developed specialized cable-laying ships, underwater cable designs, and signal amplification systems. The successful 1866 cable established reliable communication between Europe and North America for the first time in history.
Moreover, submarine cable technology required innovations in electrical insulation, signal transmission, and cable handling that pushed existing technologies to their limits. Cable manufacturing demanded systematic quality control and testing procedures that ensured reliable performance under extreme conditions. Successful cable companies developed integrated capabilities that combined advanced materials, precision manufacturing, and specialized installation techniques.
Phase 4: Imitation and Improvement (~1760s-early 1770s)
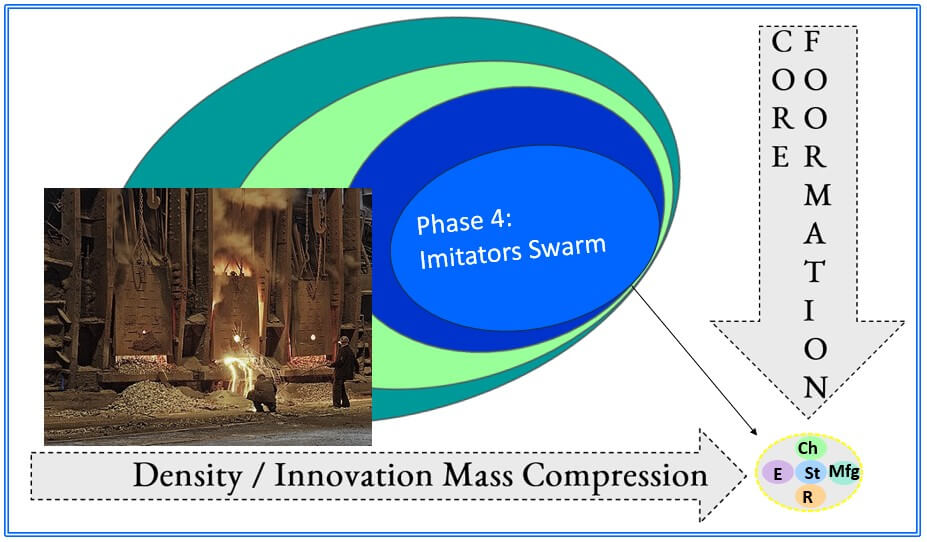
Phase 4: Imitation and Improvement
1865 – 1870
Following the initial breakthrough period, competitive forces drove systematic improvements and geographical diffusion across all the core industries, forming the nucleus of the coming third technology cycle, driven by imitators swarming.
Pictured on the left is an example of an Open Hearth Process. Siemens-Martin utilized this alternative steel production method using scrap materials(1865-1867).
Companies developed enhanced technologies while expanding production capabilities to serve growing markets.
Steel Production Enhancements
The Siemens-Martin open hearth process, introduced in 1865, provided an alternative to Bessemer steel production with superior quality control capabilities. This method allowed steelmakers to use scrap steel as raw material while producing higher-grade steel for specialized applications. Open hearth furnaces offered greater flexibility in steel composition and quality than Bessemer converters.
Consequently, steel companies began specializing in different market segments based on their production capabilities. Some facilities focused on high-volume structural steel for railroad and construction applications. Others developed specialized steel grades for machinery, tools, and precision applications. This specialization drove further innovations in steel chemistry and production techniques.
Electrical System Improvements
Werner von Siemens’ dynamo enhancements in 1867 significantly improved electrical generator efficiency and reliability. His innovations included better magnetic field designs, improved armature construction, and more effective electrical connections. These improvements made electrical power generation practical for industrial applications beyond telecommunications.
Furthermore, electrical equipment manufacturers began developing systematic approaches to DC power distribution and utilization. Industrial facilities installed electrical lighting systems that provided superior illumination compared to gas or oil alternatives. Electrical motor development progressed rapidly as manufacturers recognized electricity’s potential for industrial power applications.
Heavy Manufacturing Innovations
Early steam turbine designs during the 1860s promised revolutionary improvements in power generation efficiency. These devices converted steam energy directly into rotational motion without the reciprocating mechanisms that limited traditional steam engines. Turbine development required precision manufacturing techniques and advanced materials that pushed existing capabilities.
Additionally, precision manufacturing techniques spread throughout the machinery industry as companies recognized standardization’s competitive advantages. Interchangeable parts reduced maintenance costs and improved equipment reliability. Systematic manufacturing approaches enabled companies to serve larger markets while maintaining quality standards.
Railroad Infrastructure Modernization
Steel rail implementation between 1865 and 1870 systematically replaced iron infrastructure with superior materials that could handle increasing traffic loads. Steel rails lasted significantly longer than iron alternatives while supporting heavier trains and higher speeds. Railroad companies coordinated massive replacement projects that required careful scheduling and resource management.
Simultaneously, railroad bridge construction evolved to take advantage of steel’s superior strength-to-weight ratio. Engineers designed longer spans and higher load capacities that improved route efficiency and reduced construction costs. Steel bridge construction required new engineering techniques and construction methods that established industry standards.
Telegraph Network Expansion
Multiple competing telegraph companies created systematic coverage across national and international routes between 1865 and 1870. Competition drove technological improvements in signal transmission, message handling, and network reliability. Telegraph operators developed standardized procedures and equipment that enabled seamless communication across different company networks.
Additionally, telegraph technology improvements included better insulation materials, more reliable transmission equipment, and enhanced signal amplification systems. Network expansion required systematic approaches to route planning, equipment installation, and operational coordination. Successful telegraph companies developed integrated capabilities that ensured reliable service across extensive networks.
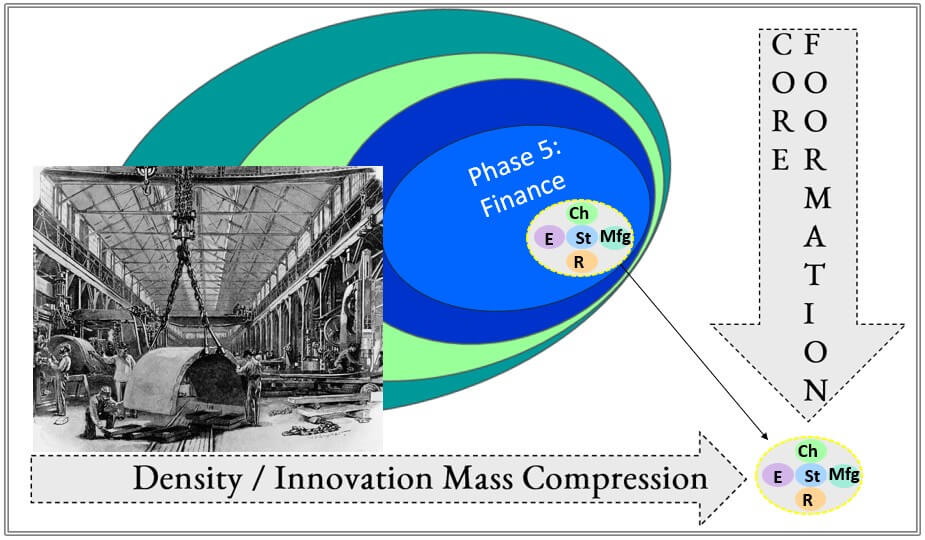
Phase 5: Financial Reorientation Toward Industrial Ventures
1870 to 1875
The final phase of the Core Formation Period witnessed fundamental changes in capital allocation as financial markets recognized the core industries’ transformative potential.
On the left, Carnegie Steel Company Integrated Production Systems (1870-1875) is shown. This image depicts vertical integration, which combines mining, smelting, and rolling operations. This was all brand new.
Investment patterns shifted decisively toward integrated industrial development. The shift created large-scale corporate model for industrial organization.
Steel Industry Consolidation
Andrew Carnegie’s systematic approach to integrated steel production required massive capital investments that transformed industry structure. His operations controlled every aspect of steel production from raw materials to finished products, achieving unprecedented efficiency and quality. Carnegie’s success demonstrated that steel industry leadership required comprehensive integration rather than specialized operations.
Similarly, other steel entrepreneurs developed integrated operations that combined mining, transportation, and manufacturing capabilities. These companies required enormous capital investments for blast furnaces, rolling mills, and supporting infrastructure. Financial markets began recognizing steel companies as fundamental infrastructure investments rather than specialized manufacturing ventures.
Electrical Equipment Manufacturing
Specialized electrical equipment manufacturing attracted significant investment capital as markets recognized electricity’s commercial potential. Companies developed integrated capabilities for generator production, electrical component manufacturing, and system installation. Electrical equipment manufacturing required precision tooling, specialized materials, and systematic quality control that traditional craftwork could not provide.
Furthermore, electrical companies began developing comprehensive systems that integrated power generation, distribution, and utilization equipment. These companies required substantial capital for research and development, manufacturing facilities, and market development. Investment patterns reflected growing recognition of electricity’s transformative potential across multiple industries.
Industrial Machinery Investment
Capital flows toward precision manufacturing equipment reflected growing recognition of machinery’s role in industrial productivity. Companies invested heavily in machine tools, steam engines, and specialized manufacturing equipment that enabled systematic production of consistent products. Industrial machinery investment required long-term capital commitments that traditional financing methods could not support effectively.
Additionally, machinery manufacturers developed integrated capabilities that combined design, manufacturing, and service functions. These companies required substantial investments in engineering talent, manufacturing facilities, and customer support systems. Financial markets began recognizing machinery companies as essential infrastructure providers rather than specialized equipment suppliers.
Railway Financing Systems
Systematic capital mobilization for continental railroad construction created new financial instruments and investment approaches. Railroad companies required unprecedented capital amounts that exceeded traditional financing capabilities. Investment banking evolved to handle the scale and complexity of railroad financing requirements.
Moreover, railroad investment attracted international capital. For example, investors recognized the American railroad development’s transformative potential. European investors provided substantial capital for American railroad construction, while American investment techniques influenced European railroad development. Railroad financing established precedents for large-scale infrastructure investment that other industries adopted.
Chemical Industry Capitalization
Systematic capital allocation for industrial chemistry and materials production reflected growing recognition of chemicals’ role in industrial development. Chemical companies required significant investments in research and development, specialized equipment, and quality control systems. Chemical industry development demanded integrated approaches that combined scientific research with systematic manufacturing capabilities.
Consequently, chemical companies attracted investment capital from sources that recognized chemistry’s applications across multiple industries. Chemical products served textile, metalworking, explosives, and pharmaceutical applications that drove sustained demand growth. Investment patterns reflected understanding of chemicals’ fundamental role in industrial processes.
Communication Infrastructure Investment
Capital mobilization for systematic telegraph and early telephone networks required new approaches to infrastructure financing. Communication companies needed substantial investments in equipment, installation, and network development that traditional financing could not support. Communication infrastructure investment attracted capital from sources that recognized information transmission’s commercial value.
Furthermore, international communication projects required coordination between multiple financial markets and regulatory systems. Submarine cable projects demanded particularly sophisticated financing approaches that managed technical, commercial, and political risks. Communication infrastructure investment established precedents for international technology ventures.
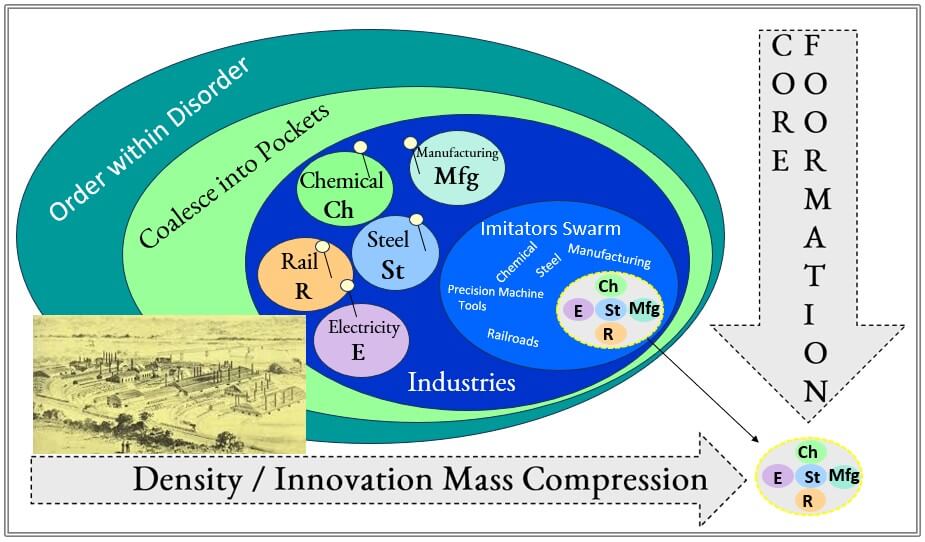
Summary for the third technology cycles gestation period
1840s to 1870s
The five phases of the Core Formation Period created comprehensive foundations for the 1875 Installation Period across all the core industries. This systematic development process transformed scattered innovations into integrated industrial capabilities that defined steel and electricity as the very center of the cycle.
The catalyst is shown on the left. This is an early drawing of Carnegie’s plant from the 1870s. The Big Bang for the third cycle resulted from Carnegie’s opening of his Bessemer plant in Pittsburgh in 1875.
This would define the character of the third technology cycle. The period demonstrates how technological paradigms emerge through coordinated development rather than individual breakthrough innovations.
Integrated System Development
These thirty years established Steel, Electricity, Heavy Manufacturing and machinery, Railroads, Chemicals, and Telecommunications as the dominant paradigm for industrial development. Like the prior technology cycles, the Steel and Electrical Age required simultaneous advancement across multiple interconnected industries. Success in any single industry depended on systematic development across all related capabilities.
Capital Market Evolution
The Core Formation Period fundamentally transformed capital markets by creating investment categories recognizing industrial technology’s transformative potential. Financial institutions developed new approaches to large-scale, long-term investments that industrial development required. These financing innovations enabled the massive infrastructure projects that characterized subsequent decades.
International Coordination Requirements
The emerging industrial system demanded unprecedented international coordination as companies developed continental and intercontinental operations. Technology transfer, resource allocation, and market development required systematic cooperation between organizations in different countries. This international integration established precedents for global industrial development.
Transition to Installation Period
By 1875, the Core Formation Period had established all necessary foundations for the great steel and electrical infrastructure boom. The systematic industry development of the preceding thirty years created the technological capabilities, financial resources, and organizational systems that massive expansion required. The Installation Period’s dramatic growth reflected the comprehensive preparations of the Core Formation Period.
Historical Significance
The steel and electrical core cycle demonstrated increasing complexity and systematic integration to prepare a super-dense technological core. Structurally, it was very similar to previous technology cycles; however, its history was very different. As we explore the third cycle and how it unfolds, we will see three nations leading the technology cycle for the first time—something that had never happened before.
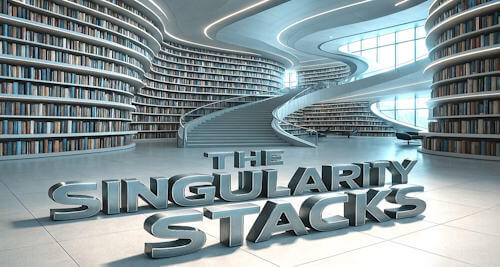
Link to the publications that created the core for the third technology cycle.
The innovations reference library section lists the inventions from the Perezian Cycles in the Periods in which they occurred. The link is below:
The Innovations and Reference Library for the Third Technology Cycle.
The main entrance to Technology Cycles Main Library – The Singularity Stacks Link
The picture of the Stacks is a hotlink as well
The next phase: The Installation irruption