Core Formation Cycle Four

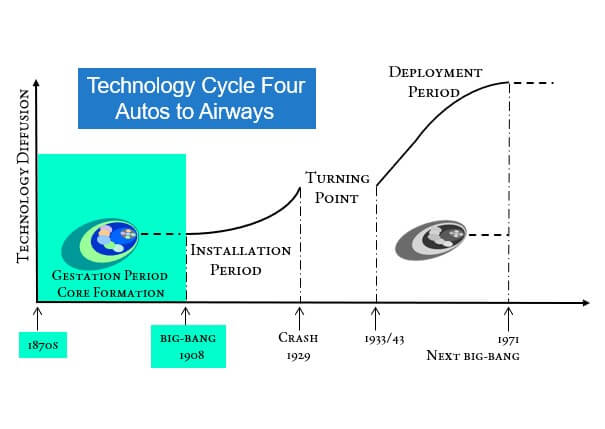
The Core Formation Period of the Fourth Technology Cycle (1870s-1900s):
The period from 1870 to 1900 represents one of technological history’s most crucial yet under-examined eras. Within Carlota Perez’s framework of Technology Cycles, these decades constitute the Core Formation Period of the Fourth Technology Cycle, known as the Automobile Age (1908-1974). The revolution that the internal combustion engine fostered is well known. While historians have extensively documented the dramatic transformations that followed—explosive automobile growth, oil industry expansion, steel production scaling, and mass production adoption—they have paid far less attention to the foundational innovations that made these revolutionary changes possible.
This essay argues that the Core Formation Period of 1870-1900 provided not merely a prelude to the automobile age but the essential foundation upon which the entire Fourth Technology Cycle stood.
Through five distinct phases—Initial Ripples, Coalescence to solve bottlenecks, Emergence of New Industries, Imitation via Schumpeter’s technology swarming, imitation, and Improvement, and the final phase the Financial Reorientation. This period developed core technologies, business models, financial instruments, and institutional frameworks that would enable revolutionary transformation in transportation, energy, materials, and manufacturing.
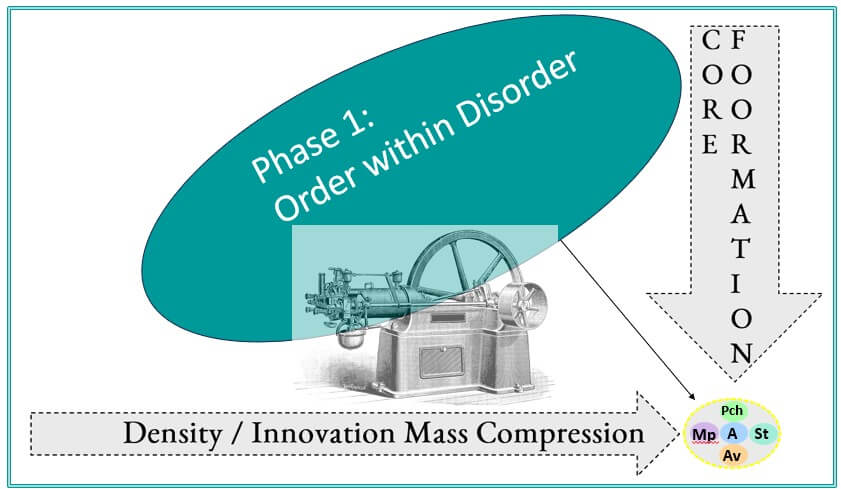
Phase 1: Initial Ripples – Seeming Unrelated Innovations
1870-1875
Pictured on the left after 14 years of research and development, Otto succeeded in creating the compressed charge internal combustion engine May 9, 1876
In 1876, Nicolaus August Otto found a way to layer the fuel mixture into the cylinder, causing the fuel to burn progressively, for stationary use. Pictured on the left is an 1880s rendering of the American Otto engine.
Building upon Étienne Lenoir’s earlier gas engine work, Otto’s design dramatically improved power-to-weight ratios crucial for automotive applications.
Automobile Technology Foundations
Nikolaus Otto developed the four-stroke internal combustion engine in 1876, creating the period’s most significant innovation. Otto’s engine solved the fundamental problem of converting chemical energy into mechanical power efficiently and reliably. The four-stroke cycle—intake, compression, power, exhaust—provided optimal balance of power, efficiency, and reliability for mobile applications.
Simultaneously, carburetor technology advanced through pioneers like Siegfried Marcus, whose float carburetor in 1870 provided systematic fuel metering and air-fuel mixture control essential for practical engine operation.
George Brayton developed his constant-pressure engine in 1872, demonstrating alternative approaches to internal combustion, while early experimenters like Camille Alphonse Faure and Gaston Planté worked with electric motors that would later provide groundwork for automotive electrical systems. Steam car experimenters like Sylvester Roper and others contributed mechanical engineering knowledge applicable to all vehicle types.
Petrochemical – Oil Industry Foundations
Edwin Drake’s 1859 Pennsylvania oil drilling success continued influencing industry development throughout the 1870s. Engineers refined rotary drilling techniques that improved upon Drake’s cable tool methods, enabling exploration in diverse geological conditions. This technological development proved essential for later expansion to Texas and California.
Companies refined kerosene production methods, establishing the oil industry’s economic foundation. Companies like Standard Oil invested heavily in refining technology, developing expertise that would later support gasoline production. Early experimenters treated gasoline as a kerosene refining byproduct, creating technical knowledge crucial when automobile development generated automotive fuel demand.
Companies established oil transportation systems that laid groundwork for integrated supply chains. Engineers developed pipeline technology, railroads built connections to oil fields, and manufacturers developed tanker cars, creating transportation infrastructure necessary for industry expansion. Geologists discovered oil in California, Texas, and other regions, identifying formations supporting future massive production increases.
Steel Industry Advances
Henry Bessemer continued refining his steel-making process through the 1870s, addressing technical challenges limiting adoption. His improvements in process control, quality consistency, and production efficiency made Bessemer steel economically competitive while providing superior performance characteristics.
William Kelly independently developed pneumatic steelmaking, validating fundamental principles while contributing additional process optimization insights. Manufacturers developed crucible steel techniques that provided high-quality alternatives for specialized applications, creating diversified technological bases serving different market segments.
The Siemens brothers and others experimented with different furnace designs, contributing to metallurgical process understanding enabling specialty steel grade development. Companies improved iron ore processing methods that addressed quality and consistency challenges, while metallurgists developed specialized steel alloys, demonstrating potential for tailoring steel properties through composition control.
Aviation Precursors
Aviation developers established scientific foundations for powered flight. George Cayley’s continued influence through disciples maintained research momentum, while Alphonse Pénaud’s rubber-powered model aircraft in 1871 demonstrated practical stability principles and control mechanisms.
Francis Wenham and others developed aerodynamic theory that provided scientific foundations in the late 18th century. Wenham established the first wind tunnel in 1871, creating experimental tools for systematic aerodynamic research. Photographers like Eadweard Muybridge and Étienne-Jules Marey studied bird flight, providing unprecedented documentation of flight mechanics.
Mass Production Foundations
Companies like Singer Sewing Machine Company, Colt’s Patent Fire Arms, and Waltham Watch Company developed interchangeable parts manufacturing, demonstrating systematic production methods. Brown & Sharpe and Pratt & Whitney refined precision measuring tools, creating technical capability for consistent, high-quality component production.
Manufacturers improved machine tool accuracy by providing precision production equipment. Companies developed specialized machinery that addressed specific industry requirements while contributing to a general understanding of the manufacturing process. Early experimenters with continuous production demonstrated the potential for dramatic efficiency improvements through process optimization.
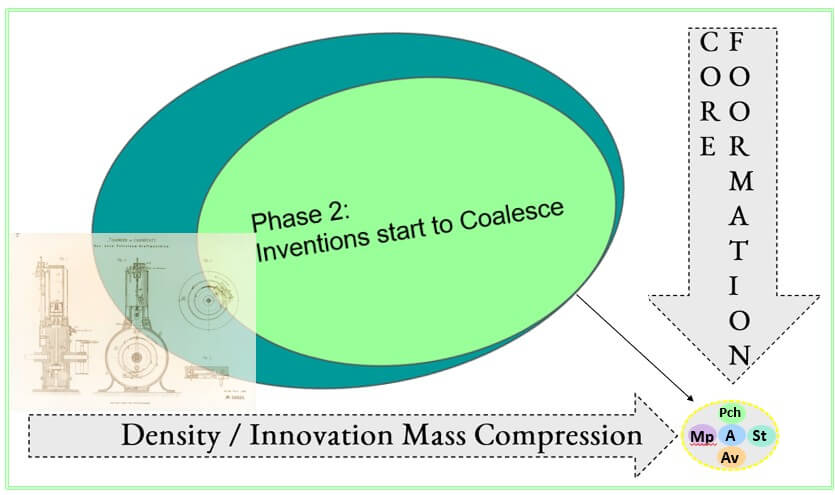
Phase 2: Coalescence to Solve Bottlenecks
1875-1885
Key step on the way to the four-wheeled automobile
Today, the drive system is the key to the modern automobile, just as it was in the pioneering days of motorization. For this reason, the engine with a single vertical cylinder – patented by Gottlieb Daimler on 3 April 1885 (German Patent DRP 34926) – was an enormously key invention (pictured on left).
The second phase witnessed systematic attempts to integrate individual innovations into coherent technological systems, addressing specific bottlenecks that limited practical application.
Automobile Development Integration
Karl Benz created the Patent-Motorwagen (1885-1886), representing successful integration of internal combustion engine technology with wheeled vehicle design. This achievement required systematic solution of integration challenges preventing earlier motorized transportation attempts, successfully combining Otto’s engine with purpose-designed chassis, transmission, and steering systems.
Gottlieb Daimler developed high-speed engines that addressed power-to-weight ratio limitations. Operating at 900 RPM versus Otto’s 180 RPM, Daimler’s engine achieved dramatic power output improvements per unit weight. Wilhelm Maybach innovated carburetor designs that solved fuel metering challenges enabling reliable operation across varying conditions.
Engineers developed transmission systems that addressed power characteristic matching between engines and vehicles. Manufacturers created belt drives, chain drives, and early gear transmissions, providing a mechanical advantage for converting engine power into vehicle motion. Companies improved tire technology, providing cushioning and traction necessary for practical operation.
Oil Industry Consolidation and Efficiency
John D. Rockefeller’s Standard Oil pursued vertical integration that addressed multiple operational bottlenecks. By acquiring refineries, pipelines, and transportation systems, Standard Oil controlled entire value chains while optimizing operations across business phases and capturing profit margins at each stage.
Companies developed pipeline networks that dramatically reduced transportation costs. Engineers constructed long-distance pipelines providing efficient alternatives to railroad transportation with significant cost advantages, greater reliability, and increased capacity. Refineries improved efficiency through continuous distillation, improved fractionation, and waste heat recovery, increasing efficiency while improving product quality—Standard Oil standardized products, creating consistency necessary for large-scale markets. The company implemented quality control procedures ensuring consumer reliability while companies developed bulk storage and distribution systems addressing logistical challenges of managing large petroleum product quantities.
Steel Industry Capacity and Quality Solutions
Andrew Carnegie adopted the Bessemer process at Edgar Thomson Steel Works, demonstrating successful vertical integration from iron ore mining through steel manufacturing. This enabled cost control, removed production bottlenecks, and ensured manufacturing quality.
Henry Clay Frick improved coke production methods ensuring consistent quality while reducing costs. Companies expanded steel production capacity through new integrated plant construction, creating additional capacity while incorporating latest technology improvements.
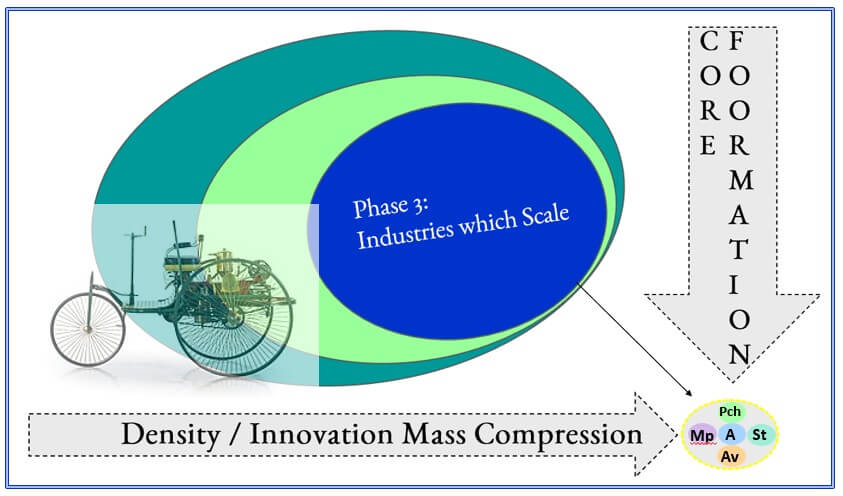
Phase 3: Emergence of New & Revolutionized Industries
1885-1892
Pictured on the left is an early prototype of the Benz Patent-Motorwagen (“patent motorcar”), built in 1885 by the German engineer Karl Benz. It is widely regarded as the first practical automobile and was the first car put into production. It was patented in January 1886 and unveiled in public later that year.
The third phase marked technological system crystallization into recognizable industries with distinct companies, markets, and competitive dynamics.
Automobile Industry Emergence
The Benz Patent-Motorwagen (“patent motorcar”), built in 1885 by the German engineer Karl Benz, is widely regarded as the first practical automobile and was the first car put into production. It was patented in January 1886 and unveiled in public later that year.
Karl Benz established Benz & Cie in 1883, marking the world’s first automobile manufacturing company birth. The Patent-Motorwagen’s commercial success demonstrated that automobiles could serve as reliable, practical products rather than experimental curiosities, establishing market foundations for industry development.
Companies developed automobile manufacturing techniques that established production methods later scaled for mass production. Skilled craftsmen provided technical knowledge and quality standards for systematization and automation. Companies established dealership and sales networks, creating distribution infrastructure necessary for commercial success.
International agreements like Panhard et Levassor’s Daimler licensing enabled global automobile industry establishment. Countries developed patent systems creating intellectual property frameworks supporting innovation while facilitating technology transfer.
Oil Industry Geographic Revolution
Discoveries in Texas, California, and other regions broke Pennsylvania’s production monopoly, creating diversity enabling massive production increases. Regional companies established operations providing competitive alternatives to Standard Oil dominance while serving local markets.
I.C. White developed petroleum geology as a scientific discipline, providing theoretical exploration foundations. His anticlinal theory (1885) established geological principles guiding oil exploration for decades. Companies developed long-distance transportation systems connecting diverse production regions with refining centers.
Steel Industry Corporate Revolution
Major corporations like Carnegie Steel Company formed in 1892, representing fundamental shifts from individual ownership to corporate organization, enabling capital and management resource mobilization for large-scale production.
Companies pursued vertical integration strategies encompassing raw materials through distribution, creating cost control and quality assurance while providing competitive scale economies. Investment banks developed steel industry financing providing capital market access while creating financial structures for industrial consolidation.
Mass Production Revolution
Ransom Olds conducted assembly line experiments at Olds Motor Vehicle Company, demonstrating dramatic productivity improvement potential through systematic production organization. Companies developed continuous production methods representing fundamental shifts from batch to flow manufacturing.
Engineers integrated specialized machinery with production processes, achieving precision and consistency necessary for mass production. Companies developed production planning and control systems providing organizational methods for complex process coordination.
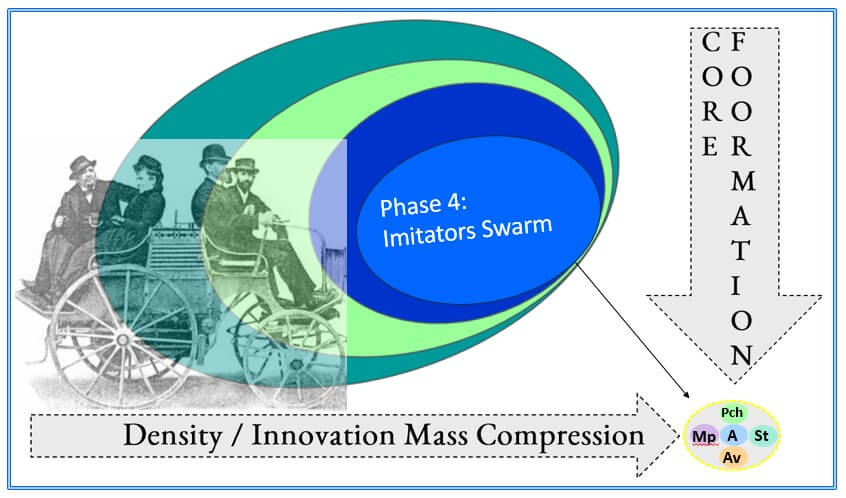
Phase 4: Imitation and Improvement
1892-1897
Émile Levassor and Armand Peugeot of France began producing vehicles with Daimler engines in 1890, laying the foundation of the automotive industry in France. Similarly, Emile Roger, a Parisian bicycle manufacturer, built Benz engines under license for several years and then began selling Benz automobiles (many built in France).
The fourth phase witnessed widespread innovation diffusion accompanied by continuous refinement and local adaptation, with geographic expansion and systematic improvement through competitive pressure.
Automobile Technology Diffusion
International licensing agreements accelerated worldwide automobile development. Multiple countries established automobile manufacturing creating competitive pressures driving continuous improvement while fostering innovation through competition.
Émile Levassor and Armand Peugeot of France began producing vehicles with Daimler engines in 1890, laying the foundation of the automotive industry in France. Similarly, Emile Roger, a Parisian bicycle manufacturer, built Benz engines under license for several years and then began selling Benz automobiles (many built in France).
Companies improved automobile reliability and performance through competitive pressures and user feedback. Manufacturers developed comfort and convenience features reflecting growing market demand understanding, while companies expanded market segments demonstrating diverse application potential.
Oil Industry Geographic Expansion
Companies adapted oil drilling techniques to different geological conditions, enabling production expansion to new regions. Regional companies developed refining and distribution networks creating competitive Standard Oil alternatives while serving regional markets effectively.
Companies improved oil exploration methods essential for new resource identification and production capacity expansion. Refineries expanded petroleum product lines reflecting growing petroleum chemistry understanding and new application development.
Steel Industry Process Expansion
Companies adopted open-hearth furnace technology providing superior quality control and raw material flexibility. Metallurgists developed specialized steel grades addressing emerging industry requirements while demonstrating product differentiation potential through metallurgical control.
Companies expanded steel production capacity through new construction and modernization, creating regional competition while serving growing markets. Companies improved quality control and testing methods essential for building customer confidence.
Mass Production Adoption
Companies adopted mass production techniques across industries, demonstrating systematic production method broad applicability. Manufacturers developed specialized equipment achieving precision and consistency necessary for large-scale manufacturing.
Companies improved production planning and control systems providing organizational methods for complex manufacturing process coordination. Companies expanded techniques across industries through technology transfer and workforce mobility.
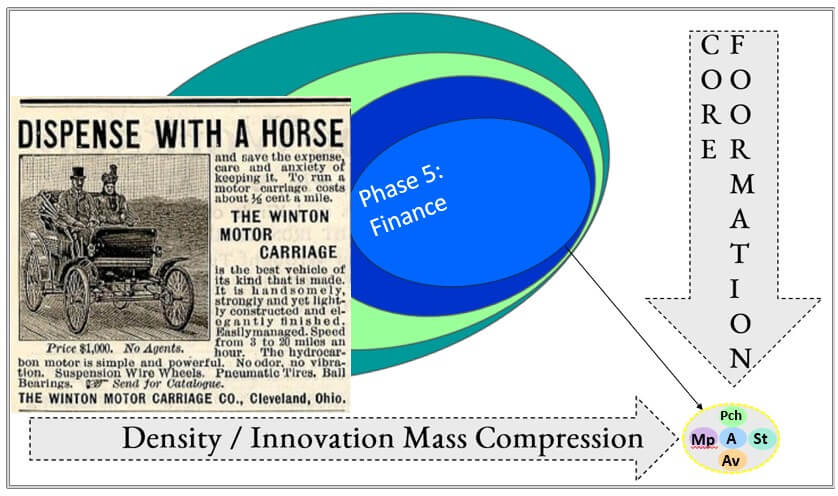
Phase 5: Financial Reorientation Toward Industrial Ventures
1897-1900
The final phase witnessed fundamental financial market shifts as capital increasingly flowed toward industrial ventures rather than traditional investments, providing capital resources for massive industrial production scaling.
Major investors formed automobile investment syndicates like Winton Motor Carriage Company (1897), pictured in a newspaper article on the left, demonstrating systematic capital mobilization for industry development.
Automobile Industry Investment
Major investors formed automobile investment syndicates like Winton Motor Carriage Company (1897), demonstrating systematic capital mobilization for industry development. Investors formed Electric Vehicle Company with $200 million capital, representing ambitious large-scale automobile enterprise attempts.
Companies developed automobile industry financing mechanisms establishing financial infrastructure for growth. Investors created venture capital arrangements, companies issued stock offerings, and investment banks established relationships providing capital market access while creating business expansion financial structures.
Oil Industry Financial Consolidation
J.P. Morgan’s involvement in oil industry financing represented major financial institution engagement in industrial development. Companies developed oil industry corporate finance establishing financial structures for large-scale operations through corporate organization, stock and bond markets, and investment banking relationships.
Oil industry companies established large-scale capital projects, demonstrating the financial market’s ability to support major industrial infrastructure development. Companies financed pipeline construction, developed refineries, and established distribution networks requiring significant capital investments.
Steel Industry Financial Integration
Negotiators created U.S. Steel Corporation (1899-1900), representing the most dramatic financial reorientation example. The $1.4 billion capitalization made it the world’s largest corporation while demonstrating massive capital mobilization potential for industrial development.
Companies developed steel industry corporate finance establishing financial structures for large-scale operations. Companies established large-scale capital projects demonstrating financial market ability to support major industrial development.
Financial Market Transformation
Wall Street shifted investment focus from railroads to industrial companies, representing fundamental American financial market transformation. Companies developed industrial stock markets establishing financial infrastructure for industrial development through stock exchanges, investment banking services, and financial analysis methods.
Investment banks established industrial banking creating financial intermediaries for large-scale development. Investors developed industrial venture capital establishing financial mechanisms for supporting innovation and entrepreneurship.
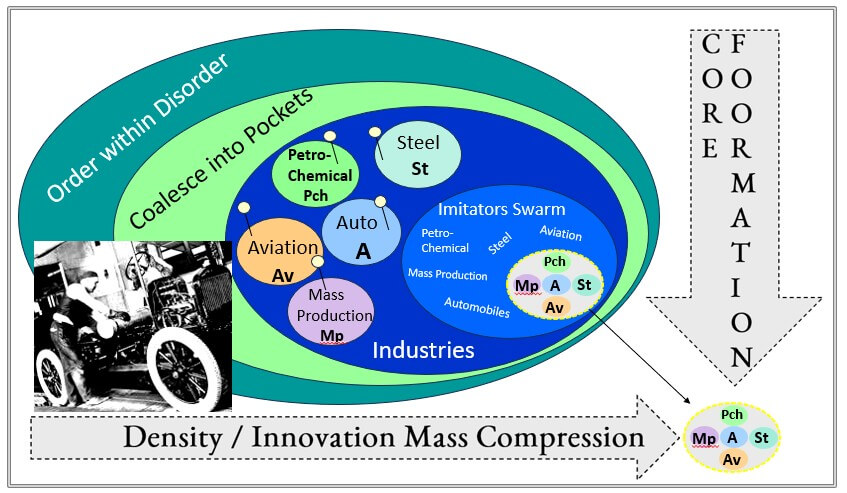
Summary for the fourth technology cycles gestation period
1870s to 1908
The Core Formation Period featured unprecedented technological convergence and cross-industry fertilization as parallel innovations began reinforcing each other. Steel improvements enabled stronger, more reliable automobile engines while creating new specialty steel markets. Petroleum products provided automotive fuel while serving as petrochemical raw materials.
The catalyst is shown on the left. The photograph is of a Ford employee working on the assembly line in the River Rouge plant. The Big Bang for the fourth cycle resulted from Henry Ford adopting the assembly line in 1908. Ford further put every facet of production in the enormous River Rouge facility.
Companies rapidly adapted manufacturing techniques developed for one industry across multiple sectors. Machine tool innovations served both steel and auto industries simultaneously, creating efficiency improvements across entire manufacturing sectors. Steel production and petroleum refining materials science advances supported both automotive and aviation development.
Infrastructure and Institutional Development
The period witnessed essential institutional and infrastructure foundation development for Fourth Technology Cycle success. Educational institutions established technical education programs creating skilled workforces for advanced manufacturing. Governments developed patent systems establishing legal innovation infrastructure while professionals formed engineering societies creating technical knowledge sharing frameworks.
Companies established industrial research laboratories providing systematic innovation foundations. Financial institutions developed specialized instruments providing industrial development financial infrastructure while companies established testing and standards laboratories creating quality assurance technical infrastructure.
Geographic and International Dimensions
The Core Formation Period featured unprecedented international dimensions as technological development transcended national boundaries, creating the first truly global industrial system. Regional innovation concentration created industrial clusters benefiting from shared infrastructure and knowledge spillovers.
Countries facilitated international technology transfer, skilled workers immigrated carrying expertise, and companies established patent licensing agreements creating global innovation networks accelerating technological development. American companies exported industrial techniques demonstrating global influence while international cooperation established patterns characterizing mature industrial development.
Social and Economic Context
Growing urbanization created concentrated markets for new solutions while providing necessary labor forces. The expanding middle class created consumer markets for mass production while educational developments supported technical training. Cultural attitudes toward technological progress provided social acceptance for new technology adoption.
Labor movements influenced manufacturing innovation while creating efficiency improvement pressures. Companies resolved quality control, safety, environmental, and regulatory challenges, demonstrating the importance of addressing technological adoption barriers.
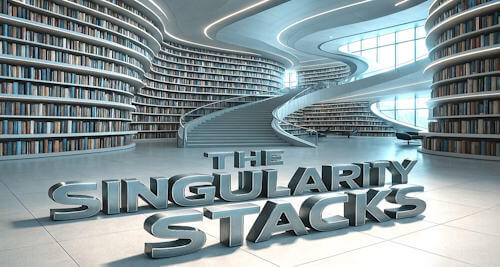
Link to the publications that created the core for the fourth technology cycle.
The innovations reference library section lists the inventions from the Perezian Cycles in the Periods in which they occurred. The link is below:
The Innovations and Reference Library for the Fourth Technology Cycle.
The main entrance to Technology Cycles Main Library – The Singularity Stacks Link
The picture of the Stacks is a hotlink as well
The next phase: The Installation irruption